From its previous understanding as an obscure element, selenium has become an intriguing component of health, disease, as well as many industrial processes.
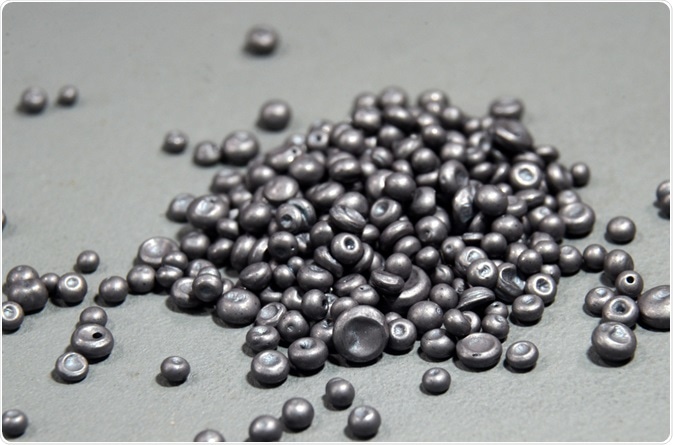
Image Credit: Kim Christensen / Shutterstock.com
Sources of selenium
Selenium can be found in 75 minerals, some of which include crooksite and clausthalite. Notably, selenium rarely exists in its pure form in nature.
Most of the selenium in use today originates from the anode slime generated during the electrolytic refining of copper. Anywhere from 30 to 80% of the contained selenium may be retrieved, either by smelting the residue with soda ash or roasting with soda ash.
There are various other techniques that can be used to obtain selenium, such as roasting with fluxes in order to convert selenium into its volatile oxide, which is then recovered from the flue gas. Alternatively, selenium is calcined into a soluble form which may be leached out.
More than 80% of the selenium in the world is produced in refineries located in Belgium, Japan, Canada, and the United States. Commercial grade selenium is 99.5% pure.
Selenium is also recovered from industrial scraps, such as discarded photocopy machine photoreceptor drums. Taken together, these scraps account for 15% of the production of refined selenium. Secondary sources of selenium are responsible for the production of 250 tons a year.
Roasting with soda ash
The major reaction steps involved in the roasting with soda ash, which is the primary method used to produce selenium, include:
- Roasting of anode mud from which copper has been removed, with soda ash, to yield the selenite and the selenate of sodium
- Leaching out selenium with water
- Neutralization of the leached solution in order to remove tellurium as a precipitate
- Sparging of the leached solution with sulfur dioxide to yield precipitated selenium
The yielding of precipitated selenium is achieved through the following steps:
- Anode mud is mixed with silica and soda ash after the removal of copper. This mixture is then smelted.
- The slag contains various metallic impurities such as iron and silica, which are removed.
- Air is forced through the molten charge to produce volatile selenium oxide, which can be separated from the solid residues. These are further treated to extract various precious metals.
- The soda ash is now leached out using water, and the leached solution filtered to remove the solid waste.
- Neutralization of the filtered leached solution removes tellurium as a precipitate
- Acid is added to the remaining solution to precipitate selenium
- The precipitate, which contains selenium, is now boiled, washed, dried, and finally powdered to yield selenium.
Mining Tellurium (Te) and selenium (Se) for solar panels - University of Leicester
Purification of selenium
Selenium is prepared from a solution of the impure selenium in sodium sulfite, which is then filtered to remove the solid waste. Acidification of the filtrate precipitates the selenium, which then undergoes purification by distillation to produce high-grade elemental selenium.
In these processes, elemental selenium in its red amorphous form is removed from the settling tanks and elsewhere. This form of elemental selenium is then coked using steam and hot water, which results in a gray crystalline form of the element that is referred to as coked selenium. Coken selenium can be used to prepare commercial grade selenium by drying, grinding, and grading by size.
For higher grades of purity, distillation is used. High-grade selenium is more than 99.999% pure, and is used in thermoelectric devices.
References
Further Reading