3D bioprinting involves the precise printing of biocompatible materials, cells, growth factors, and other essential elements required to create intricate and functional living tissues. Several forms of tissue, including skin, bone, vascular grafts, and cartilage structures, have been produced via 3D bioprinting.
Various materials and formulations can be employed to produce both rigid and flexible tissues according to specific requirements. Although several 3D printing techniques exist, extrusion-based methods using bioinks are the most commonly chosen due to the sensitivity of the materials involved.
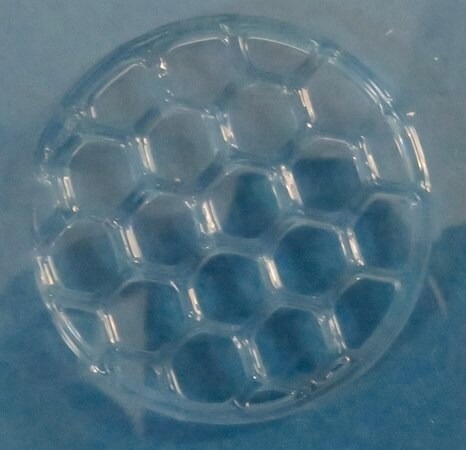
Image Credit: Merck
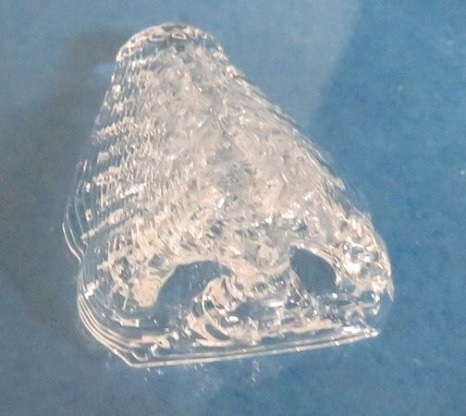
Image Credit: Merck
Properties
Source: Merck
. |
. |
Description |
0.2 μm sterile filtered, Suitable for 3D bioprinting applications |
Form |
Viscous liquid |
Impurities |
≤5 CFU/g Bioburden (Fungal)
≤5 CFU/g Bioburden (Total Aerobic) |
Color |
Colorless to pale yellow |
pH |
6.5-7.5 |
Application(s) |
3D bioprinting |
Storage temp. |
2-8 °C |
Application
Polaxomer is a thermos-responsive hydrogel that has been employed in bioprinting and tissue engineering as a mold, track patterning, and sacrificial material. Due to the nature of micellar-packing gelation, which allows it to be moved and transferred easily, it is regarded as one of the best printable hydrogels.
Furthermore, the viscosity of TissueFab®- Sacrificial bioink is stable at both room and human body temperatures, which means it can print at both room temperature and physiological temperature. TissueFab®- Sacrificial Bioink becomes liquid at 4 °C and dissolves in aquatic settings, enabling its use as a sacrificial material for creating channels and vasculature in tissue engineering applications.
Packaging
The product comprises 10 mL of solution in a glass container.
Other notes
Important guidelines for achieving the best bioprinting outcomes
- Adjust printing conditions (nozzle size, speed, pressure, temperature, cell density) to suit your printer and application.
- Prevent bubble formation in bioink. Handle it carefully during mixing and transfer; avoid excessive shaking or vortexing.
Procedure
- Prepare bioink: To avoid gelation, keep TissueFab® - Sacrificial Bioink on ice and gently flip the bioink to create a homogenous solution. Do not vortex or shake. TissueFab® - Sacrificial Bioink should be placed in the selected printer cartridge.
- Bioprint: To promote gelation, warm TissueFab® - Sacrificial Bioink in the printer cartridge to room temperature for 10–15 minutes. Follow the manufacturer’s instructions for the 3D printer. Load the 3D printer’s print cartridge and print straight onto a Petri dish or multi-well plate. Flow should be adjusted based on nozzle diameter, printing speed, printing pressure, and temperature. Using extra printheads, TissueFab® - Sacrificial Bioink can be produced alongside cell-laden bioinks.
- Optional crosslink: If additional bioinks are employed, crosslink the bioprinted structure before removing the sacrificial scaffold by following instructions.
- Remove sacrificial scaffold: Cool the printed structure for at least 5 minutes at 4 °C. Perfuse or rinse with cold PBS.
- Culture cells: Follow standard tissue culture protocols to cultivate the bioprinted tissue with a suitable cell culture medium.