Fine powders and granular materials are extensively used in industrial applications. To manage and to enhance processing techniques, these materials have to be exactly characterized. The characterization techniques are connected either to the properties of the grains (granulometry, chemical composition, morphology, etc.) and to the behavior of the bulk powder (density, flowability, electrostatic properties, blend stability, etc.).
However, concerning the physical behavior of bulk powder, most of the methods used in quality control or R&D laboratories are based on traditional measurement methods. During the past 10 years, Granutools has updated these methods to match the current requirements of production departments and R&D laboratories. Specifically, the measurement processes have been automatized and demanding initialization techniques have been formulated to gain reproducible and interpretable results. Furthermore, the use of image analysis methods enhances the precision of the measurements.
A range of measurement techniques has been developed to meet all the requirements of industries processing granular materials and powders. However, in this article, the focus will be on the GranuHeap and GranuFlow instruments.
The main goal of this article is to provide some indications to a customer keen on knowing about the GranuFlow and to describe the best aperture in order to achieve a flow. For this purpose, Granutools decided to pair the heap shape analysis (static angle of repose, measured by the GranuHeap) to the minimum aperture to realize a flow in the GranuFlow. However, it is essential to note that there is no direct connection between those two measurements techniques. The aim is to answer the following question:
“If my powder achieves a Static Angle of Repose of 60°, will this product flow through the GranuFlow apertures?”
Material and Methods
Powders Selection
Five different samples were chosen for this article:
- InhaLac is a superior quality crystalline lactose powder, developed for DPIs
- One food product, a fat milk powder
- A glass beads powder made up of spherical particles
- One stainless-steel 316L product developed by LPW for additive manufacturing (Selective Laser Melting process)
- One Polyamide 12 powder developed by Arkema for additive manufacturing (Selective Laser Sintering process)
Table 1. Powders classification.
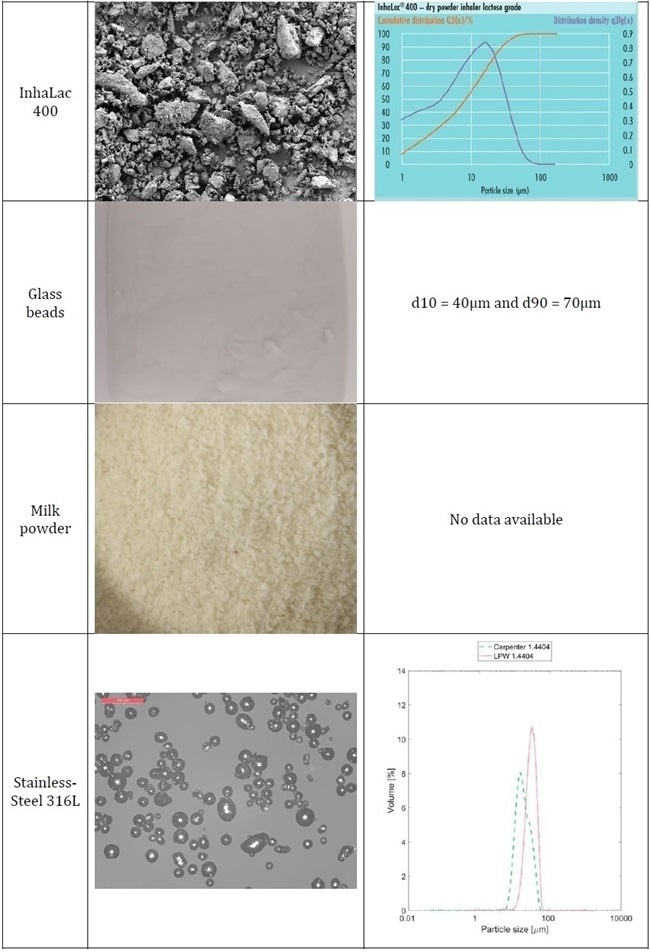
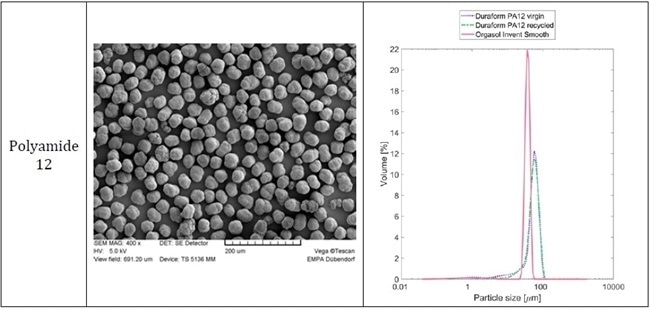
All the experiments were performed at the same temperature/humidity environments (RH = 42.0% ± 1.5% and T = 21.3 ± 1.0 °C).
GranuHeap
A heap is formed when a powder is poured onto a surface. It is established that both the repose angle and the heap shape strongly rely on grain properties. Specifically, a cohesive powder forms an uneven heap, while a non-cohesive powder forms a steady conical heap. Thus, a precise measurement of the heap shape offers beneficial information about the physical properties of the powder sample.
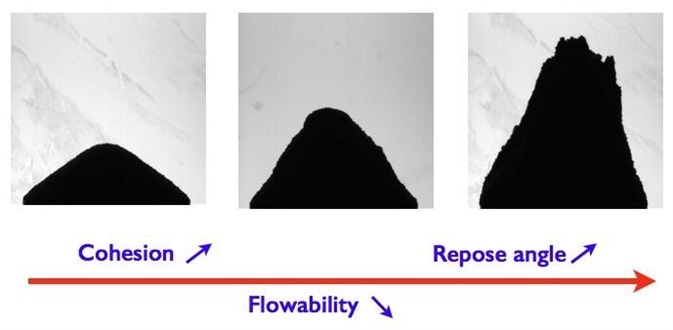
Figure 1. Sketch of GranuHeap measurement principle.
GranuHeap instrument is an automated heap shape measurement technique based on image processing and examination. A powder heap is developed on a cylindrical support. In order to obtain reproducible results, an initialization tube with an inner diameter equal to the circular support is set up on the support. After filling the initialization tube manually with a specified volume of powder (usually 100 mL), the tube goes up at the constant speed. Thus, the powder flows from the tube to create a heap on the cylindrical support. A regulated rotation of the support enables attaining various heap projections matching diverse heap orientations.
A custom image recognition algorithm establishes the position of the powder/air interface. The repose angle indicates the angle of the isosceles triangle with the same surface than the powder heap projected image. This isosceles triangle matches the ideal cohesiveness heap shape. The repose angle is calculated for each image, i.e., for each heap orientation. Later, an averaged value is calculated. Generally, if the repose angle is lower, the powder flowability is better.
The deviation between the real heap interface and the isosceles triangular heap delivers the static cohesive index. The static cohesive index is calculated for each image, i.e., for each heap orientation. Later, an averaged value is calculated. This static cohesive index is close to zero for a non-cohesive powder and grows when the cohesive forces within the powder strengthen. The table below recapitulates the empirical relation between the results acquired with powder flowability and GranuHeap instrument.
Table 2. Flowability classification as a function of angle of repose and cohesive index.
Flow |
Repose Angle (°) |
Static Cohesive Index |
Excellent |
25-30 |
< 0.2 |
Good |
31-35 |
0.3 - 0.5 |
Fair |
36-40 |
0.6 – 0.8 |
Passable |
41-45 |
0.9 – 1.2 |
Poor |
46-55 |
1.3 – 1.7 |
Very poor |
56-65 |
1.8 – 2.4 |
Very very poor |
>66 |
> 2.5 |
For each experiment using the GranuHeap instrument, the 40 mm diameter support was chosen. To increase measurements accuracy, 16 pictures were captured during the heap rotation (1 picture each 11.25°). At the end of the examination, one last picture is captured to check the pile integrity when the measurement is carried out. Just the average angle of repose (in degrees) and the standard deviation will be taken into consideration.
GranuFlow
GranuFlow instrument is a laboratory hopper related to an electronic balance linked to a computer. The flow rate is measured as a function of the aperture sizes D to get a flow curve. The aperture size is adjusted easily using a rotating device. Lastly, the flow curve is equipped with a theoretical model to extract the key parameters: the minimum aperture size Dmin and the Beverloo parameter C correlated to the flowability of the sample.
The mass flowrate F via a circular orifice of diameter D is given by the product of the mean speed of the grains <vout>, the aperture area, and the bulk density ρ. One has the standard expression:
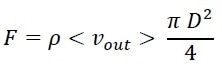
The Beverloo’s law is founded on two hypotheses:
- The flow is obstructed when the orifice diameter is below a threshold Dmin.
- The grains experience a free fall prior to passing through the orifice, i.e., vout = √2 g β D . This relation comes from the notion that the jamming mechanism is because of the formation of a semi-spherical arch before the orifice. If this arch has a standard size proportional to the aperture, β = 0.5 is obtained. To be more wide-ranging, the parameter β can be a free parameter.
Lastly, the mass flowrate expression turns out to be:

In this article, the GranuFlow was used to establish the minimum diameter to acquire a flow.
Experimental Results
The histogram below shows the static angle of repose (in degrees) on the left y-axis and the minimum diameter (in mm) to attain a flow using the GranuFlow for the five chosen powders. However, the minimum tested diameter for this article was 2 mm.
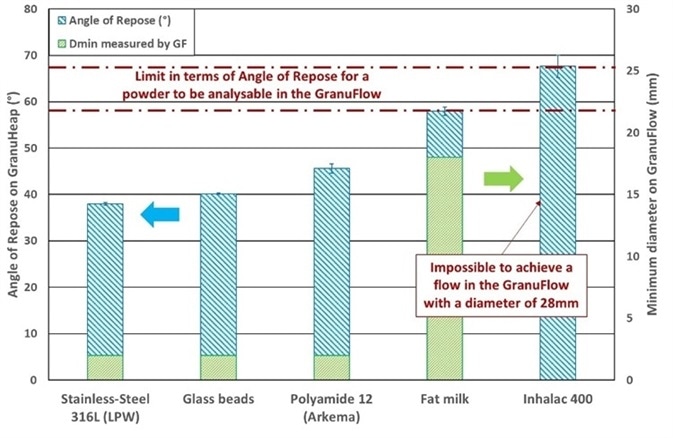
Figure 2. Angle of repose measured with the GranuHeap and minimum diameter to achieve a flow with the GranuFlow for the five selected powders.
Table 3. Examples of pictures taken using GranuHeap
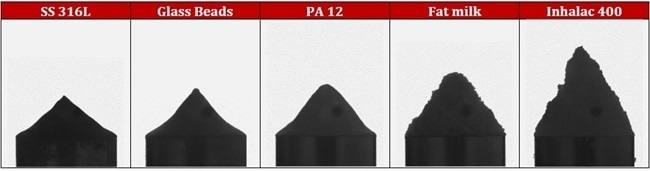
Those outcomes show that only the Inhalac 400 was not examined with the GranuFlow because no flow was noted using an aperture of 28 mm. However, for the stainless-steel 316L, polyamide 12, glass bead, and fat milk powders, it was possible to note a flow in the GranuFlow. Thus, using a powder with a static angle of repose of 58°, a flow is accomplished with an 18 mm aperture size, but a powder with a static angle of repose of 68°, no flow was noted. Accordingly, if the measured powder angle of repose is below 58°, the GranuFlow can examine this powder.
Conclusions
This article shows that if a customer’s powder realizes a static angle of repose lower than 58° in the GranuHeap, this powder can be examined using the GranuFlow.
Certainly, it is evident that static angle of repose and flow through an aperture are not directly connected. For example, the SS316L powder and the glass beads sample accomplish approximately the same angle of repose, but the SS316L powder mass flowrate is a lot higher than that of the glass beads. In other words, powder density will also play a crucial role in vertical geometry. Fundamentally, if the powder density is more, the minimum diameter becomes lower to attain a flow in the GranuFlow.
Bibliography
- Cascade of granular flows for characterizing segregation, G. Lumay, F. Boschin, R. Cloots, N. Vandewalle, Powder Technology 234, 32-36 (2013).
- Combined effect of moisture and electrostatic charges on powder flow, A. Rescaglio, J. Schockmel, N. Vandewalle and G. Lumay, EPJ Web of Conferences 140, 13009 (2017).
- Compaction dynamics of a magnetized powder, G. Lumay, S. Dorbolo and N. Vandewalle, Physical Review E 80, 041302 (2009).
- Compaction of anisotropic granular materials: Experiments and simulations, G. Lumay and N. Vandewalle, Physical Review E 70, 051314 (2004).
- Compaction Dynamics of Wet Granular Assemblies, J. E. Fiscina, G. Lumay, F. Ludewig and N. Vandewalle, Physical Review Letters 105, 048001 (2010).
- Effect of an electric field on an intermittent granular flow, E. Mersch, G. Lumay, F. Boschini, and N. Vandewalle, Physical Review E 81, 041309 (2010).
- Effect of relative air humidity on the flowability of lactose powders, G. Lumay, K. Traina, F. Boschini, V. Delaval, A. Rescaglio, R. Cloots and N. Vandewalle, Journal of Drug Delivery Science and Technology 35, 207-212 (2016).
- Experimental Study of Granular Compaction Dynamics at Different Scales: Grain Mobility, Hexagonal Domains, and Packing Fraction, G. Lumay and N. Vandewalle, Physical Review Letters 95, 028002 (2005).
- Flow abilities of powders and granular materials evidenced from dynamical tap density measurement, K. Traina, R. Cloots, S. Bontempi, G. Lumay, N. Vandewalle and F. Boschini, Powder Technology, 235, 842-852 (2013).
- Flow of magnetized grains in a rotating drum, G. Lumay and N. Vandewalle, Physical Review E 82, 040301(R) (2010).
- How tribo-electric charges modify powder flowability, A. Rescaglio, J. Schockmel, F. Francqui, N. Vandewalle, and G. Lumay, Annual Transactions of The Nordic Rheology Society 25, 17-21 (2016).
- Influence of cohesives forces on the macroscopic properties of granular assemblies, G. Lumay, J. Fiscina, F. Ludewig and N. Vandewalle, AIP Conference Proceedings 1542, 995 (2013).
- Linking compaction dynamics to the flow properties of powders, G. Lumay, N. Vandewalle, C. Bodson, L. Delattre and O. Gerasimov, Applied Physics Letters 89, 093505 (2006).
- Linking flowability and granulometry of lactose powders, F. Boschini, V. Delaval, K. Traina, N. Vandewalle, and G. Lumay, International Journal of Pharmaceutics 494, 312–320 (2015).
- Measuring the flowing properties of powders and grains, G. Lumay, F. Boschini, K. Traina, S. Bontempi, J.-C. Remy, R. Cloots, and N. Vandewall, Powder Technology 224, 19-27 (2012).
- Motion of carbon nanotubes in a rotating drum: The dynamic angle of repose and a bed behavior diagram, S. L. Pirard, G. Lumay, N. Vandewalle, J-P. Pirard, Chemical Engineering Journal 146, 143-147 (2009).
- Mullite coatings on ceramic substrates: Stabilisation of Al2O3–SiO2 suspensions for spray drying of composite granules suitable for reactive plasma spraying, A. Schrijnemakers, S. André, G. Lumay, N. Vandewalle, F. Boschini, R. Cloots and B. Vertruyen, Journal of the European Ceramic Society 29, 2169–2175 (2009).
- Rheological behavior of β-Ti and NiTi powders produced by atomization for SLM production of open porous orthopedic implants, G. Yablokova, M. Speirs, J. Van Humbeeck, J.-P. Kruth, J. Schrooten, R. Cloots, F. Boschini, G. Lumay, J. Luyten, Powder Technology 283, 199–209 (2015).
- The flow rate of granular materials through an orifice, C. Mankoc, A. Janda, R. Arévalo, J. M. Pastor, I. Zuriguel, A. Garcimartín and D. Maza, Granular Matter 9, p407–414 (2007).
- The influence of grain shape, friction and cohesion on granular compaction dynamics, N. Vandewalle, G. Lumay, O. Gerasimov and F. Ludewig, The European Physical Journal E (2007).
About Granutools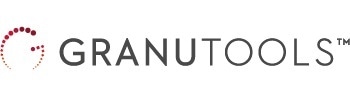
GranuTools, is a company that improves powder understanding by delivering leading edge physical characterization tools.
“All we do is powder flow characterization”
A Set of Complementary Tools
Combining decades of experience in scientific instrumentation with fundamental research on powders characterization, we offer a unique set of complementary instruments for granular materials characterization.
Named after their purpose, our instruments are tools to understand macroscopic behavior of powders.
GranuFlow for flow, GranuHeap for static cohesion, GranuDrum for dynamic cohesion, GranuPack for tapped density and GranuCharge for triboelectric charge measurements are designed with the following in mind:
- Precise & Repeatable
- Automatic
- No Operator Dependency
- Robust & Easy to Use
- Clear Interpretation