Fluid bed systems have been utilized in the pharmaceutical industry for numerous years. The addition of an aqueous or alcoholic granulation medium agglomerates the dry powder particles. This fluid contains a volatile solvent that can be removed through drying.
Top-spray fluidized bed solutions have been the predominant choice for a long time. However, top-spray granulators are gradually being replaced with tangential spray nozzle systems as their advantages become clearer. L.B. Bohle offers a range of fluid bed granulation systems suitable for both small-scale production and production-scale research and development.
L.B. Bohle: Granulation Technology / Fluid Bed Technology: Bohle Fluid Bed System BFS
Video Credit: L.B. Bohle Maschinen und Verfahren GmbH
Granulation with the Bohle Fluid Bed Granulator
L.B. Bohle uses the Bohle Uni Cone BUC® process to optimize fluid bed
The patented Bohle Uni Cone BUC® is a slotted air distributor plate with a conical displacement cone. This configuration ensures comprehensive fluidization of particles. The resultant tangential motion of particles facilitates the formation of a uniform film, for example, on pellets, without the occurrence of twins.
Since the fluidized particles or granules move tangentially at relatively low fluidization height, they do not require a high-volume expansion. This efficiency translates into a reduced requirement for installation height, saving both space and costs on the production floor.
The BFS system includes a minimum of six filter elements, each of which can be individually cleaned to ensure a constant airflow through the product bed.
Drying, granulation, and coating without the need for alteration
Another advantage of the tangential design of L.B. Bohle facilities is that granulation, coating, and drying can all be performed in one system, eliminating the need to reconfigure equipment between processes.
The BFS fluid bed system can be enhanced with an online moisture measurement system utilizing NIR technology (similar to infra-red analysis). This advanced feature enables the precise and reproducible identification of the moisture level in real-time during the granulation and drying stages.
Comparison of fluidized bed equipment
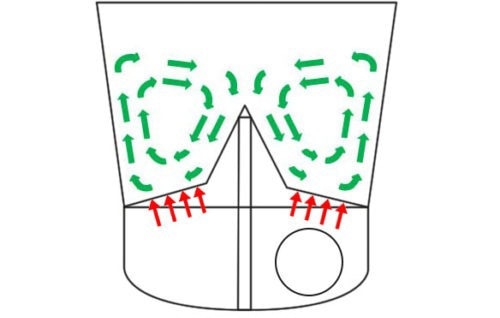
Groundbreaking Bohle Uni Cone BUC®-Technilogy. Image Credit: L.B. Bohle Maschinen und Verfahren GmbH
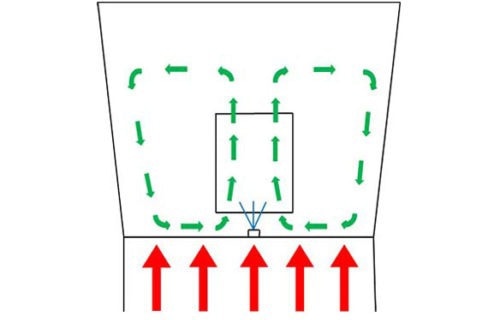
Ordinary Wurster Process. Image Credit: L.B. Bohle Maschinen und Verfahren GmbH
Benefits Bohle Uni Cone BUC®
- Effective air distribution: Quite narrow particle size distribution and formation of spherical granules
- Frameless product bottom plate design: Fast and simple cleaning
- Inspection of air plenum through the back pipe: Cross-contamination prevention in the bowl inlet
- Filter inspection: Safe position for the operator to stand on the floor
- Handling of the bottom plate: Safe de-installation in combination with an in-wall built lifting column

Bohle Uni Cone BUC® Tangential Spray. Image Credit: L.B. Bohle Maschinen und Verfahren GmbH
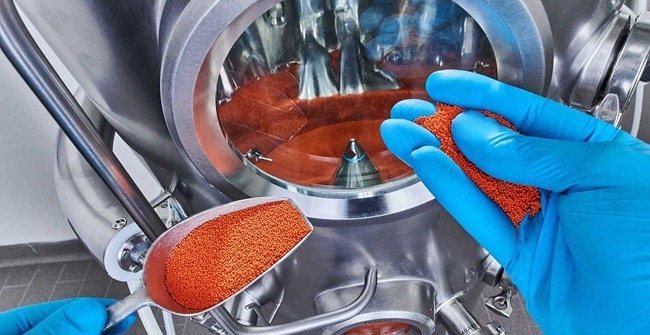
Image Credit: L.B. Bohle Maschinen und Verfahren GmbH
Benefits of the fluid bed granulator
- Lowering of filters via electric drive
- Complete fluidization of particles
- Pressure surge resistance up to 12 bar- optimum conditions for containment applications
- Patented filter cleaning – patented diffuser
- Even film coating, no twin formation
- Low installation height, efficient space utilization
- Integration of PAT, NIR, and WIP
- Easy-to-remove distributor plate
Variations and technical features
Fluid bed systems are available from L.B. Bohle in various sizes and technological configurations.
The following list gives an overview and comparison of the various fluidiz bed units used for granulation.
Source: L.B. Bohle Maschinen und Verfahren GmbH
BFS series |
Qty. of product filter bags |
Height of the fluidized bed system [mm] |
Number of nozzles (tangential spray) |
Control system |
BFS 30 |
4 |
ca. 1980 |
1 |
PLC controlled, Touchpanel operated |
BFS 60 |
6 |
ca. 2930 |
2 |
PLC controlled, Touchpanel operated |
BFS 120 |
6 |
ca. 3600 |
3 |
PLC controlled, Touchpanel operated |
BFS 240 |
9 |
ca. 3920 |
4 |
PLC controlled, Touchpanel operated |
BFS 360 |
12 |
ca. 4570 |
5 |
PLC controlled, Touchpanel operated |
BFS 480 |
10 |
ca. 4990 |
6 |
PLC controlled, Touchpanel operated |