One of the most complex product cycles in the world is pharmaceutical pipelines. Each aspect of drug discovery and its development processes needs to be rigorously conducted to guarantee commercial success.
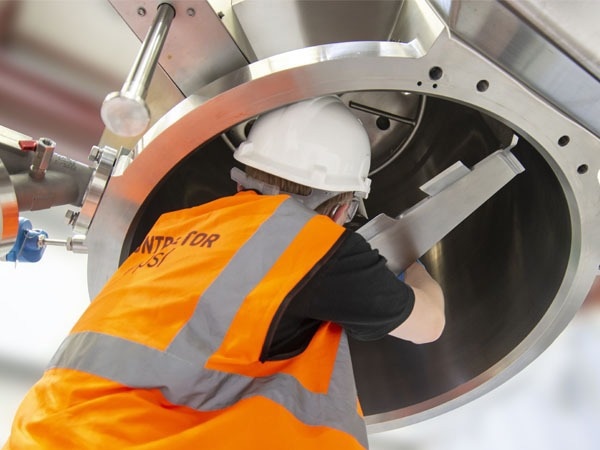
Image Credit: Powder Systems
With the interlinking and complex aspects of the drug pipeline, routine processes can, however, be easily overlooked. One frequently neglected area is preventative maintenance.
Embracing a preventative mindset and establishing a consistent maintenance schedule is essential for minimizing the risk of equipment failure, which can lead to workforce disruption and production errors. However, preventative maintenance goes beyond averting severe disruptions; it also promotes process efficiency and enables better budget management.
This article will outline the top four benefits of preventative maintenance for pharmaceutical manufacturers.
1. Reduced risk of unplanned downtime
Upgrades or machine repairs are unavoidable; however, by making use of a preventative maintenance program, repairs can be scheduled at convenient times.
One of the most difficult aspects of maintaining pharmaceutical equipment is the variety of equipment available. Each machine is different and will need to be maintained based on the process it is used for, its impact on the process, and what parts it comprises.
Implementing a preventative maintenance plan enables tracking of scheduled servicing for specific equipment. Unplanned downtime can abruptly halt production, resulting in significant financial losses for businesses, including repair expenses and employee salaries.
2. Increased efficiency
Planned maintenance allows process managers to schedule additional tasks during the equipment ‘downtime’. This can limit disruptions and increase efficiency across the business.
Regular maintenance also enhances equipment efficiency as parts are cleaned, lubricated, and replaced as needed, thereby improving the quality of their output.
It is also important to note that crucial spare parts are frequently overlooked in pharmaceutical maintenance plans. These spare parts must be monitored, maintained, and easily accessible for replacement if needed. Neglecting this aspect can result in a single crucial part causing process interruptions and incurring avoidable costs for the company.
3. Extended asset lifespans
Given the substantial investment in pharmaceutical machinery, planned maintenance is indispensable for extending its lifespan. Properly maintained equipment operates for longer periods and delivers higher-quality performance compared to neglected machinery.
Time-based preventive maintenance can assist in predicting when a piece of equipment requires inspection or needs to be replaced based on elapsed running time. This limits the risk of equipment being worn down to failure.
4. Better budget management
One of the most significant benefits of preventative maintenance is cost savings.
Scheduled maintenance can be monitored so that machinery can be serviced based on production output or running time, and damage can be treated before equipment failure. Compared to unplanned maintenance, this option saves time and money.
Furthermore, complex process equipment typically has specialized custom-made parts that can take weeks or even months to manufacture. As a result, stock control becomes a chief aspect of preventative maintenance and must always be managed.
When machinery breaks down, repair costs will be much higher as resolving the issue could involve specialist technicians, express delivery of necessary parts, and loss of production.
In the worst-case scenario, equipment that lacks regular maintenance may suffer a complete breakdown, necessitating replacement at significantly higher costs compared to routine maintenance and partial replacements. Unplanned shutdowns that last as little as just a few days can still result in profit losses surpassing the capital cost of acquiring a brand-new system.
Tailored aftercare service and support
Equipment that is not regularly maintained may not function at its best, or it may become damaged, which is why Powder Systems Limited (PSL) offers expert aftercare support through the PSL Serve Team.
PSL assists clients with installations and can help identify critical spare parts that are recommended to be kept in stock against the machine’s lifecycle.
At PSL, introductory maintenance training is offered to both clients and their internal teams during equipment installation. This ensures they understand foreseeable maintenance needs, enabling them to incorporate this knowledge into their maintenance planning.
Furthermore, PSL’s database enables them to reach out to partners months in advance of known shutdowns, notifying them to review spare parts inventory, order critical parts well in advance, and schedule site visits around shutdown periods.
About Powder Systems 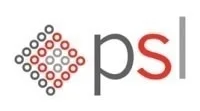
Powder Systems Limited (PSL) provides a full range of solid liquid separation solutions for filtration, drying, and processing from research and development activities up to larger commercial production scale.
Quality and innovation are central to everything they do. They are proud of their award-winning track record and have been working with industry partners for over 35 years.
PSL supports clients by developing solutions to overcome challenging manufacturing processes and provide first-class aftercare services.
Sponsored Content Policy: News-Medical.net publishes articles and related content that may be derived from sources where we have existing commercial relationships, provided such content adds value to the core editorial ethos of News-Medical.Net which is to educate and inform site visitors interested in medical research, science, medical devices and treatments.