Predicting the performance of processing equipment from measurements of powder properties is a key aim of powder processing industries.
In the powder handling industries, screw feeders are frequently used to manage a material’s flow from a hopper into a process.
The feeder’s performance is directly impacted by the properties of the powder, making it essential to customize the design of any system used to the handled product.
A poorly suited feeder and powder combination will usually be associated with low feed rates, high screw torques, and a build up of powder on the tube walls. Both long and short term operating functionality is decreased as a result of these issues.
This article outlines collaborative research undertaken by Freeman Technology (Tewkesbury, UK) and Gericke (Zurich, Switzerland) to specify powder characteristics that can be reliably analyzed in order to indicate feeder performance.
The investigation supports the value of dynamic powder characterization within this context, concluding that the production of robust models allow for the prediction of the feed rate through a screw feeder from flow properties for example Flow Rate Index (FRI), Specific Energy (SE), and Aerated Energy (AE).
These models make it easier to choose a feeder for a particular powder, predicting its probable performance with a high degree of accuracy.
Specifying Screw Feeders
Screw feeders are supplied with one or more rotating helixes or augers that are fixed within an enclosed chamber (Figure 1). Powder is transferred as the auger rotates, in line with the Archimedes screw principle which has been adjusted for material transport for centuries.
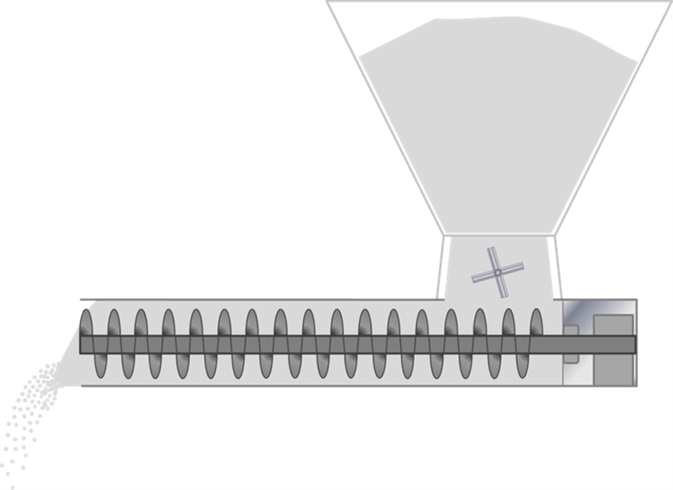
Figure 1. A screw feeder transfers powder using one of more augers enclosed in a tube. Image Credit: Freeman Technology
A range of industries utilize screw feeders, and for several decades Gericke has been consistently supplying machines for handling plastics, detergents, chemicals, construction materials, and food.
Three factors directly impact the selection and specification of every feeder. These are:
- Installation constraints related to the layout of the plant. For example, feed distances, the number of feeders, mounting requirements, and the available headroom.
- Material properties – is the material being processed adhesive, cohesive, or free-flowing, prone to attrition and fragile, fluidizable, compressible, or abrasive.
- Process requirements – whether the plant is continuously operating or is in batch mode, feed capacity, operating pressure, the extent of automation, and the required accuracy.
The size of the feeder (diameter and length), the geometry, pitch, and drive of the auger, and the accessories utilized to verify consistent flow are the key design variables that can be adjusted to meet any combination of needs.
Fluidization or agitation and vibrational feeders in the feed hopper are all viable choices. The feed rate may be managed on the basis of volume (volumetric) or weight (gravimetric).
Choosing the best screw feeder for any particular application is essential to operational efficacy for Gericke. Any feeder that is not correctly suited to the handled product is prone to be related to poor long term operation, which can present itself in many ways.
For example, flow rate may be poorly controlled or erratic, which could directly influence the total performance and efficiency of the process.
If the powder is cohesive, material accumulation inside of the equipment may be challenging, especially if there is regular product changeover and/or sensitivity to contamination from batch-to-batch.
Knowing how to characterize powders assists in predicting their performance in various kinds of equipment.
Powders are placed under a range of environments within the screw feeder, flowing gravitationally from the feed hopper into the forcing and possibly compacting the flow regime within the rotating auger(s) that moves the material forward.
The features of the powder directly contribute to the way that a powder will react to these environments. Powder characteristics have a key influence on the selection of equipment and the requirement or otherwise for tailored development.
Collaborative research between Freeman Technology and Gericke evaluated whether the characteristics analyzed using the FT4 Powder Rheometer® could be matched directly to feeder performance.
The key goal of the study was to evaluate the likelihood of predicting feeder performance from the properties of powder to accelerate the choice of an optimal screw feeder solution for any particular material.
Correlating Powder Properties with Screw Feeder Performance
To analyze the correlations between the properties of five alternate powders and their performance in two alternate screw feeders, an experimental study was performed. The following powders were investigated:
- Calcium Hydroxide
- Maltodextrin
- Calcium Citrate
- Cellulose
- Milk Protein
In the first step of the investigation, the FT4 Powder Rheometer1 was utilized to perform thorough testing of every powder sample. In each case, dynamic, shear, and bulk properties were quantified for each powder with a high level of repeatability (RSD < 5%).
To establish the volumetric flow rate (L/hr) provided at an auger rotation speed the same as 80 Hz, samples of each powder were run through both of the Gericke screw feeders. Utilizing measurements of mass flow rate (in kg/hr) and poured density, volumetric flow rate (in L/hr) was quantified.
The two screw feeders employed were a DIWE-GZD flat bottom double-screw feeder employing a 12 x 13.5 mm tube with a conical core and a DIWE-GLD-87 VR, full flight single-screw feeder employing tube No. 3.
The GZD unit is a self-cleaning, compact twin screw extruder that is utilized for applications with a low capacity, especially those appropriate for feeding materials with poor flow properties.
The GLD machine is a dynamic, compact feeder that is employed for the highly precise feeding of the majority of dry solids, for applications that need regular material changeover and those in pilot scale.
The data set analyzed for all five powders, including the average volumetric feed rate in L/hr, is presented in Table 1. To show the correlations between these two sets of data, a multiple linear regression was carried out.
This is a mathematical procedure that generates an equation to calculate a dependent (y) parameter (in this example, the volumetric flow rate) regarding influential independent (x) variables (the properties of the powder in this example).
In this equation, a p value is produced for each parameter, which suggests the likelihood that the contribution of the parameter to the relationship is statistically insignificant.
The higher the p value, the more probable that the parameter has no influence on the relationship.
A smaller p value is related to a more relevant parameter. In this investigation, a p value of 0.1 was taken as the upper limit for relevance, and parameters with p values greater than this were removed to establish a robust relationship.
GLD Feeder
Table 1. Dynamic, bulk and shear powder properties for five different powders alongside the volumetric flow rate each delivered when run through a GLD screw feeder. Source: Freeman Technology
|
Dynamic Parameters |
Bulk Parameters |
Shear Parameters |
Feeder Parameters |
Material |
BFE mJ |
SE mJ/g |
SI |
FRI |
AE40 mJ |
AR40 |
NAS s/mm |
CE50tap g/mL |
BD50tap g/mL |
CBD g/mL |
CPS % |
PD@1 kPa mbar |
PD@15 kPa mbar |
UYS kPa |
MPS kPa |
FF |
Cohesion kPa |
AIF o |
WFA o |
GLD L/hr |
Calcium Hydroxide |
354 |
6.92 |
1.30 |
2.40 |
65 |
4.1 |
0.417 |
460 |
0.538 |
0.499 |
25.2 |
14.87 |
65.3 |
5.89 |
18.21 |
3.09 |
1.525 |
35.2 |
30.8 |
185.2 |
Maltodextrin |
1282 |
5.19 |
1.11 |
1.16 |
13 |
107.3 |
0.156 |
1341 |
0.608 |
0.557 |
7.1 |
0.51 |
0.54 |
0.88 |
16.42 |
18.57 |
0.221 |
36.9 |
27.4 |
138.9 |
Milk Protein |
330 |
8.49 |
0.91 |
1.37 |
102 |
3.3 |
0.182 |
613 |
0.311 |
0.267 |
24.3 |
3.07 |
9.06 |
3.96 |
20.71 |
5.23 |
1.091 |
32.3 |
24.6 |
128.7 |
Cellulose |
630 |
8.92 |
0.87 |
1.34 |
19 |
46.0 |
0.619 |
4124 |
0.376 |
0.327 |
22.2 |
2.75 |
3.97 |
6.68 |
22.06 |
3.30 |
1.579 |
39.4 |
17.5 |
115.8 |
Calcium Citrate |
680 |
12.50 |
1.07 |
1.40 |
225 |
3.0 |
0.077 |
914 |
0.261 |
0.234 |
41.6 |
1.02 |
37.82 |
8.14 |
22.59 |
2.78 |
1.877 |
40.5 |
41.0 |
50.13 |
GZD Feeder
Table 2. Dynamic, bulk and shear powder properties for five different powders alongside the volumetric flow rate each delivered when run through a GZD screw feeder. Source: Freeman Technology
|
Dynamic Parameters |
Bulk Parameters |
Shear Parameters |
Feeder Parameters |
Material |
BFE mJ |
SE mJ/g |
SI |
FRI |
AE40 mJ |
AR40 |
NAS s/mm |
CE50tap g/mL |
BD50tap g/mL |
CBD g/mL |
CPS % |
PD@1 kPa mbar |
PD@15 kPa mbar |
UYS kPa |
MPS kPa |
FF |
Cohesion kPa |
AIF o |
WFA o |
GZD L/hr |
Calcium Hydroxide |
630 |
8.92 |
0.87 |
1.34 |
19 |
46.0 |
0.619 |
4124 |
0.376 |
0.327 |
22.2 |
2.75 |
3.97 |
6.68 |
22.06 |
3.30 |
1.579 |
39.4 |
17.5 |
34.98 |
Maltodextrin |
354 |
6.92 |
1.30 |
2.40 |
65 |
4.1 |
0.417 |
460 |
0.538 |
0.499 |
25.2 |
14.87 |
65.30 |
5.89 |
18.21 |
3.09 |
1.525 |
35.2 |
30.8 |
33.02 |
Milk Protein |
1282 |
5.19 |
1.11 |
1.16 |
13 |
107.3 |
0.156 |
1341 |
0.608 |
0.557 |
7.1 |
0.51 |
0.54 |
0.88 |
16.42 |
18.57 |
0.221 |
36.9 |
27.4 |
29.88 |
Cellulose |
330 |
8.49 |
0.91 |
1.37 |
102 |
3.3 |
0.182 |
613 |
0.311 |
0.267 |
24.3 |
3.07 |
9.06 |
3.96 |
20.71 |
5.23 |
1.091 |
32.3 |
24.6 |
18.67 |
Calcium Citrate |
680 |
12.50 |
1.07 |
1.40 |
225 |
3.0 |
0.077 |
914 |
0.261 |
0.234 |
41.6 |
1.02 |
37.82 |
8.14 |
22.59 |
2.78 |
1.877 |
40.5 |
41.0 |
10.39 |
This multiple linear regression step generated the following relationship for the GLD feeder:
Feed Rate = 49.54 FRI – 13.81 SE + 163.8
(R2 = 0.9466)
R2 is an indicator of the ‘goodness of fit’ between the data and the model with higher values nearer to the upper limit of 1, proving that there is a close fit.
This relationship implies that only two dynamic properties – specific energy (SE) and flow rate index (FRI) – out of all of the features measured are necessary to confidently predict the performance of the feeder.
While SE shows how a powder performs within an unconfined state, FRI outlines the powder’s resistance to flow variations as a function of flow rate, and is simulated by increasing or decreasing the speed of the tip of the helical blade in the powder tester.
Flow energy is calculated at a blade tip speed of 100 mm/s (as for BFE testing) and then at 70, 40 and 10 mm/s throughout FRI testing. The FRI value is the ratio of the flow energy calculated at 10 mm/s to those measured at 100 mm/s.
An FRI that is higher than one shows that the resistance to flow is greater, as demonstrated by higher flow energy, when the powder is made to flow more slowly.
All of the powders analyzed in this investigation have an FRI that is higher than one and present this shear thinning behavior.
The values predicted by the derived model and the measured flow rates for the five powders are outlined in Figure 2.
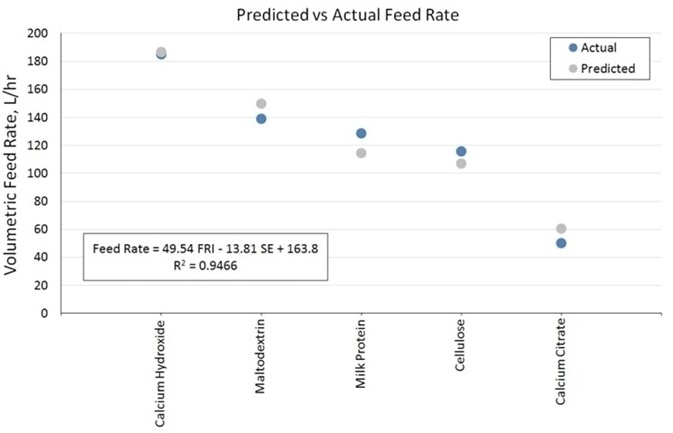
Figure 2. Predicted vs. actual feed rate data for five powders, showing the close relationship between values predicted from the GLD model using measured dynamic powder properties and those measured in the experiments. Image Credit: Freeman Technology
As indicated by the R2 value for the correlation, the predicted values precisely outline the measured performance of the powders in the GLD feeder.
Two extra powders, cement and lactose, were evaluated to test the predictive ability of the derived relationship. The calculated flow rates for each of the first five powders, the two new materials (red), and the values predicted from their powder properties are presented in Figure 3.
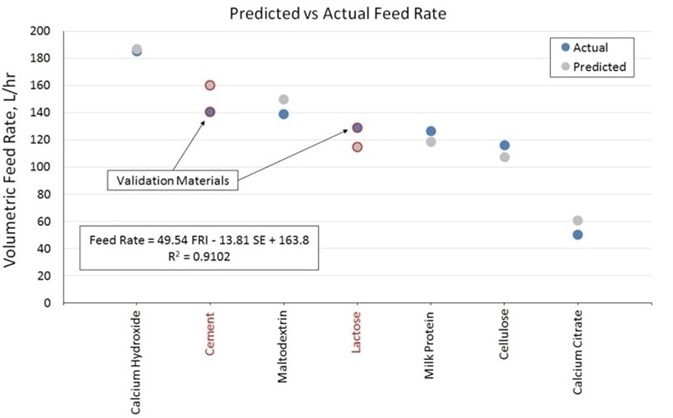
Figure 3. Predicted vs. actual feed rate data for seven powders illustrate the ability of the derived model to predict volumetric flow rate through the GLD feeder, from measurements of dynamic powder properties. Image Credit: Freeman Technology
An updated R2 verifies the close correlation between the predicted and measured flow rates for the data sets including all seven materials, and the efficacy of predicting volumetric flow rate from data on powder properties.
An identical process was carried out again to determine a correlation that could be utilized to predict performance in the GZD feeder. A more basic correlation was seen with Aerated Energy (AE), the only parameter found to be highly suitable.
Feed Rate = -0.1114 AE40 + 34.82
(R2 = 0.8383)
AE is the flow energy of the material analyzed when the sample is aerated by air traveling through it at a specified linear velocity. In this example, the determined linear velocity is 40 mm/s and the AE is AE40.
Cohesive powders often have a comparably high AW as aeration does little to decrease the resistance that they display to flow, while for free-flowing powders, AE can be close to 0 as the powders fluidize.
The materials investigated show a comparatively wide range of AE values, but a strong relationship between volumetric flow rate and AE is the same for all materials.
The measured flow rates for the values predicted by the derived model and the five powders are illustrated in Figure 4. The predicted values precisely outline the exact performance of the powders in the GZD feeder, as indicated by the R2 value for the correlation.
The investigation was extended to prove the ability of the relationship to predict the volumetric flow rate attained with cement and lactose, in the same way as the other feeder. As in the previous example, the correlation performed strongly in this predictive mode (Figure 4).
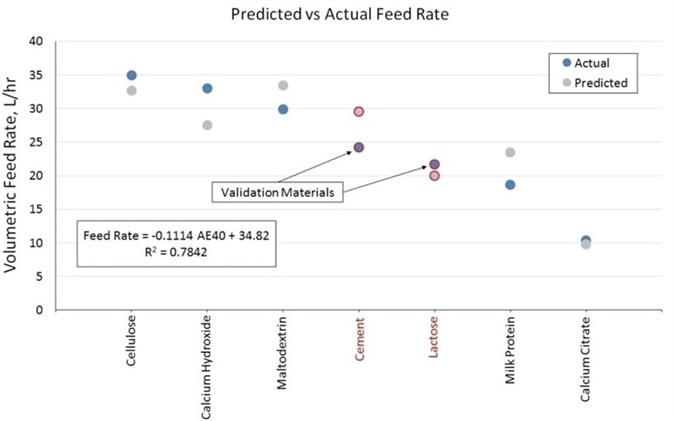
Figure 4. Predicted vs. actual feed rate data for seven powders illustrate the ability of the derived model to predict volumetric flow rate through the GZD feeder from measurements of dynamic powder properties. Image Credit: Freeman Technology
Predicting Performance
The research results demonstrate the viability of producing strong correlations between the volumetric flow rate offered by various screw feeder designs and quantifiable powder properties.
The powder is subjected to a range of process conditions by every screw feeder.
The powder’s particular attributes and the parameters found to be effective for predicting feeder performance are a reflection of this. Rather than the shear or bulk properties, it is the dynamic powder properties that were the most effective in each of the cases.
The technique used in this investigation can be applied to establish the correlations required to predict the performance of a range of powder processing equipment.
Multi-faceted powders offers the basis for such work, and assists in the specification of those properties that are most important to the performance of a powder in any given unit operation. Powder testers that support this approach can be highly beneficial for optimizing a varied range of powder processes.
References and Further Reading
1 Freeman R. “Measuring the flow properties of consolidated, conditioned and aerated powders — A comparative study using a powder rheometer and a rotational shear cell”, Powder Technology 174 (2007) 25–33.
About Freeman Technology
Freeman Technology specialises in systems for measuring the flow properties of powders and has over 15 years’ experience in powder flow and powder characterisation. The company invests significantly in R&D and applications development, and provides detailed know-how to support its range of products. Expert teams guide and support users around the world in addressing their individual powder challenges, focusing on delivering the most relevant information for the process. The result is world-leading solutions for understanding powder behaviour - in development, formulation, scale-up, processing, quality control, or anywhere that powders have a role.
Freeman Technology’s solutions include the FT4 Powder Rheometer®, a uniquely universal powder tester, and the Uniaxial Powder Tester, a complementary tool for quick and robust powder assessment. Systems are installed around the world in the chemical, pharmaceutical, toners, foods, powder coatings, metals, ceramics, cosmetics, and many other industries. They deliver data that maximise process and product understanding, accelerating R&D and formulation towards successful commercialisation, and supporting the long term optimisation of powder processes.
Freeman Technology is also the global distributor for Lenterra sensor instrumentation which provides in-line, real-time flow measurement solutions to enhance process understanding, and improve manufacturing efficiency and quality.
Founded in 1989 as a developer of automated testing systems for materials characterisation, the company has focused exclusively on powders since the late 1990s and in 2018 became part of Micromeritics Instrument Corporation The company’s R&D, manufacturing and commercial headquarters are in Gloucestershire, UK, with operations and distribution partners in key global territories.
In 2007 the company received the Queen’s Award for Enterprise in Innovation and in 2012 the Queen’s Award for Enterprise in International Trade.
Sponsored Content Policy: News-Medical.net publishes articles and related content that may be derived from sources where we have existing commercial relationships, provided such content adds value to the core editorial ethos of News-Medical.Net which is to educate and inform site visitors interested in medical research, science, medical devices and treatments.