Several challenges may be presented when processing powder blends: the blend may be prone to segregation, the creation of agglomerates may influence homogeneity, or component powders may poorly flow in the process.
In multiple applications and industries, granulation is employed to mix several components of a blend into a more homogeneous, free-flowing intermediate product for downstream processing.
The method is commonly carried out as a wet process, but the wet mass, as a result, has to be milled and dried to create a product that can be processed.
The procedure is time-consuming and expensive, and may be impossible in certain cases due to the thermal and/or chemical degradation of the active ingredient.
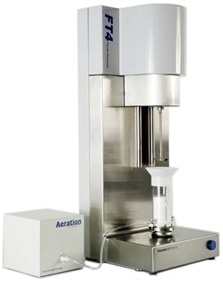
FT4 powder rheometer®. Image Credit: Freeman Technology
There are powerful advantages to dry granulation, concerning processing and cost-reduction, and it can be utilized with materials that are sensitive.
There is little known about which process parameters generate the best granulate quality to attain high-quality products and interruption-free processing. The majority of equipment suppliers and product manufacturers depend on conventional and ad-hoc trial data to specify appropriate parameters.
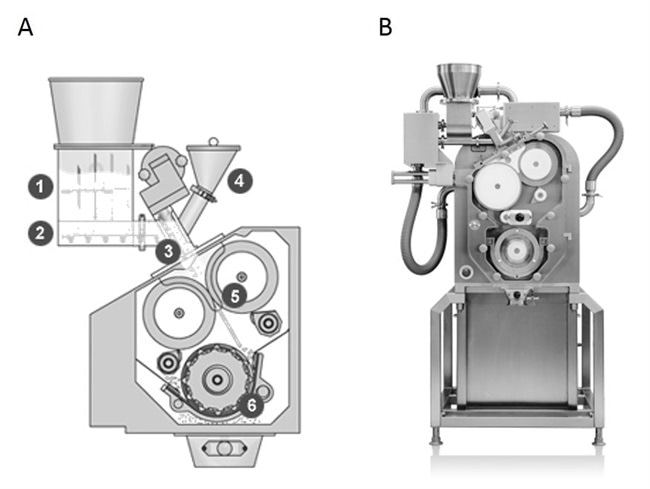
®MINI-PACTOR® roller compactor. Image Credit: Gerteis Maschinen+Processengineering AG, Switzerland
This article outlines the joint study performed by Freeman Technology Ltd. and Gerteis Maschinen+Processengineering AG, to research how the characteristics of the dry granulate of a placebo formulation are impacted by process parameters.
Methods
A Gerteis MINI-PACTOR® roller compactor, on which the compaction force, roll-gap, and roller speed can be modified along with the sieve or screen size, was employed to granulate a placebo formulation comprising of 70% lactose, 0.5% magnesium stearate, and 29.5% microcrystalline cellulose.
A Freeman Technology FT4 Powder Rheometer® was utilized to assess the produced granulates to measure the shear, bulk and dynamic properties.
The Effect of Compaction Force
Six uniform batches of the feedstock were processed in the MINI-PACTOR® at a range of compaction forces:
|
I |
II |
III |
IV |
V |
VI |
Compaction Force (kN/cm) |
3.0 |
4.5 |
6.0 |
7.5 |
9.0 |
12.0 |
A roll gap of 3 mm was preserved, the roller speed was 2.5 RPM and the screen size was kept at 1 mm. The FT4 was utilized for the ensuing analysis of the resulting six batches of granules, to assess the influence of compaction force on granule features.
Conditioned Bulk Density and Compressibility

Image Credit: Freeman Technology
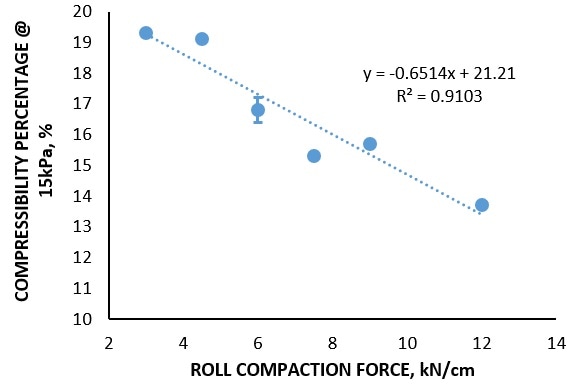
Image Credit: Freeman Technology
The linear correlations seen demonstrated that the Conditioned Bulk Density (CBD) and compressibility of the granulate adjusted with compaction force, with a higher force producing a higher CBD and lower compressibility.
More identical granules that pack more effectively, are produced by a higher compaction force. There are fewer air voids as a result of the successful packing. This enhances the bulk density of the material and means that there is less available space into which granules can move when placed under an applied stress.
Permeability
Compaction force and permeability presented a significant relationship, with a higher force producing higher permeability.
The granules created at a higher compaction force, produce a bulk that is more resistant to compaction. When an external stress is exerted on the bulk, the channels between the granules can be kept consistent, enabling air to pass through with ease.
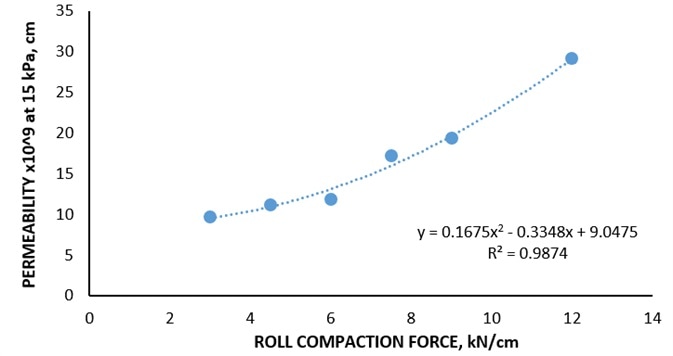
Image Credit: Freeman Technology
Based on the results, it is clear that there is a direct correlation between CBD and permeability, compressibility, and compaction force.
Compressibility decreases and the permeability and CBD of the subsequent granulate increase as the compaction force increases. All of these features are normally seen in materials that are more free-flowing and are an indication of more effective packing.
Shear properties had little influence as opposed to the bulk data and dynamic flow, with the shear cell test results offering no correlation between the wall friction angle and the compaction force, and no variation between the samples.
The absence of correlation to a low stress, dynamic process is predicted because shear cells were mostly produced to assess the onset of flow for continuous, cohesive powders under high stress.
The Effect of Roll Gap
Six uniform batches of the feedstock were processed using the MINI-PACTOR® with various roll gaps:
|
I |
II |
III |
IV |
V |
VI |
Roll Gap (mm) |
1.5 |
2 |
2.5 |
3 |
4 |
5 |
The roller speed remained constant at 2.5 RPM, the screen size was kept at 1 mm, and the compaction force at 4.5 kN/cm. An FT4 was utilized to analyze the six batches of granules produced, to discover the influence of roll gap on granule properties.
Conditioned Bulk Density
The bulk density of the granules declined as the roll gap increased, suggesting that the larger gap produces granules with a wider size distribution and less consistency.
Normally, materials with a wide PSD pack less effectively as a result of entraining a greater amount of air and decreasing the bulk density.
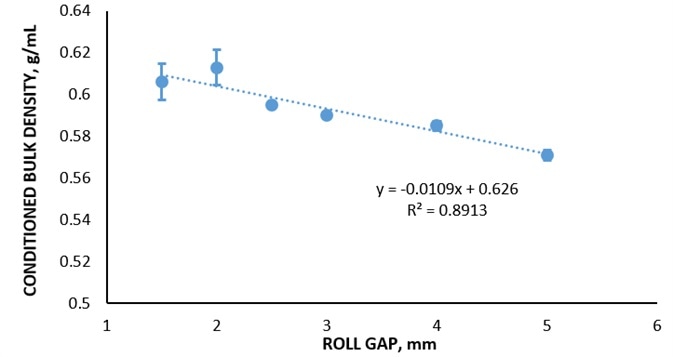
Image Credit: Freeman Technology
Consolidation Index and Permeability
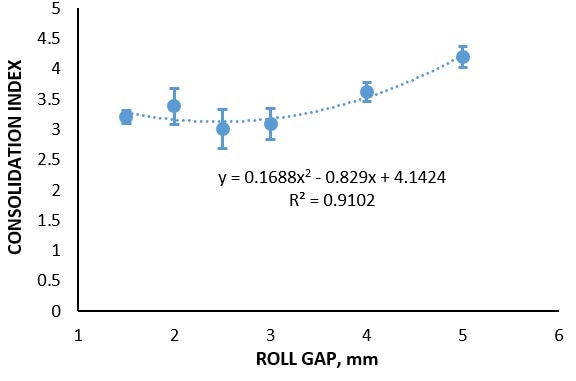
Image Credit: Freeman Technology
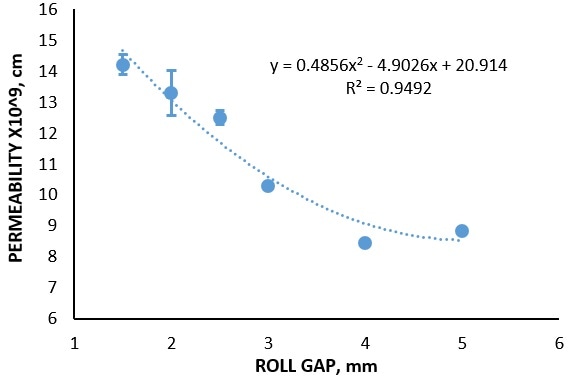
Image Credit: Freeman Technology
Robust relationships where the Consolidation Index (CI) and permeability of the granulate changed with the roll gap were also seen. A greater roll gap produced lower permeability and a higher sensitivity to vibrational consolidation.
This indicates that a bigger roll gap results in the formulation of granules with a wider particle size distribution which pack less uniformly and entrain a greater amount of air inside of the bulk.
When vibration is applied to the granules, the particles easily re-align and re-pack into a more successfully packed structure as this expels the air and results in a significant increase in flow energy.
The less uniform packing structure also does not enable consistent air channels to be made, which results in a decline in permeability.
With an increase in the roll gap, the produced granules are less homogeneous due to the less stable consolidation regime initiated between the rollers.
This can result in greater differences in surface texture, granule shape, and size distribution, brought on by the decline in particle packing efficacy as demonstrated by the higher CI value, and lower permeability and CBD values.
Variation of Compaction Force and Roll Gap
At different levels of compaction force and roll gap, nine uniform batches of the feedstock were analyzed to discover if these offered similar trends in comparison to those seen when changing only the compaction force or roll gap.
|
I |
II |
III |
IV |
V |
VI |
VII |
VIII |
IX |
Roll Gap (mm) |
1.5 |
2 |
2.5 |
3 |
4 |
5 |
1.5 |
3 |
5 |
Compaction Force (kN/cm) |
4.5 |
4.5 |
4.5 |
4.5 |
4.5 |
4.5 |
9 |
9 |
9 |
Conditioned Bulk Density and Compressibility
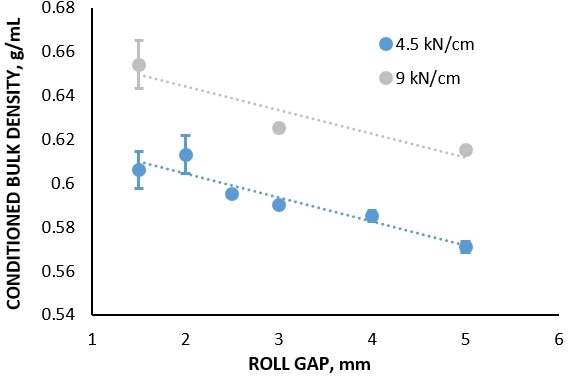
Image Credit: Freeman Technology
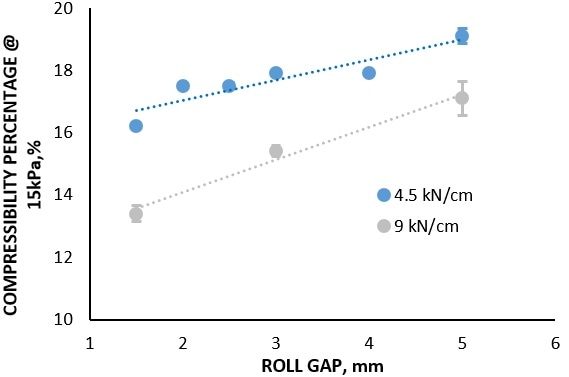
Image Credit: Freeman Technology
The granules that were created with a 9 kN/cm compaction force throughout various roll gap values repeatedly have a higher CBD and lower compressibility than those generated at 4.5 kN/cm; this verifies the observations made in the first investigations.
Comparable linear relationships were observed between roll gap and CBD at 4.5 kN/cm and 9 kN/cm compaction force. This indicates that the relationship between roll gap and CBD is not related to compaction force.
The relationship between compressibility and roll gap does not exhibit the same independence. At 9 kN/cm, compressibility displays a more pronounced increase as the roll gap increases. This indicates that the roll gap has a higher impact on granule properties at greater compaction forces.
Permeability
Granules produced at 9 kN/cm compaction force have a greater permeability compared to those produced at 4.5 kN/cm.
This suggests that the granules are more permeable and more uniformly packed when the compaction force is greater. The previously noticed relationship between permeability and roll gap was quantified by the results.
The curve is more strongly pronounced at the higher compaction force, which supports the indication that roll gap has a greater impact on granule properties at greater compaction forces.
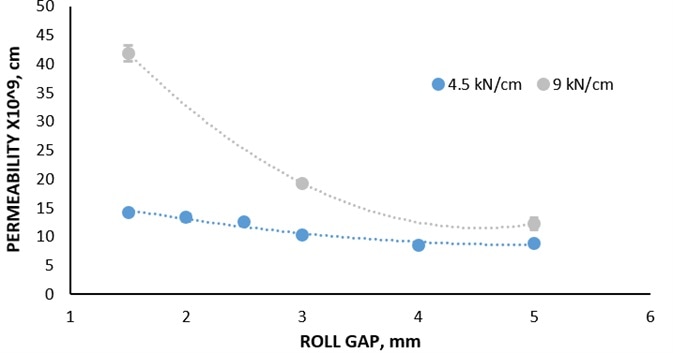
Image Credit: Freeman Technology
Conclusion
To optimize and manage process performance and verify the quality of the final product, Quality by Design explains that the relationship between materials and processes must be sufficiently understood.
From the results produced in this study, it is apparent that the necessary critical process parameters can be specified to optimize the roller compaction process to create granules with features that directly impact the performance in downstream operations and important quality characteristics of the end product.
In the flow properties analyzed by the FT4, repeatable and clear trends have been recorded, demonstrating how the process parameters impact the rheological properties of the granules in a predictable fashion.
The permeability, CBD, and compressibility demonstrated strong correlations with the modes of operation of the roll compactor.
This indicates that a mixture of a smaller roll gap and a higher compaction force is more likely to produce more stable/identical granules that form a more effectively packed powder bed, normally observed in free-flowing powders.
This investigation demonstrates the importance of powder rheology in a multivariate, comprehensive approach to powder characterization.
While it is not an essential material property, flowability can show how several properties influence the total ability of a powder to function in a specific piece of equipment.
A strong variation in process performance can happen as a result of slight changes in an individual property.
This means that multiple characterization methodologies are crucial and the results from these can be matched with process ranking in order to produce a design space with the parameters that are related to the desired process behavior.
About Freeman Technology
Freeman Technology specialises in systems for measuring the flow properties of powders and has over 15 years’ experience in powder flow and powder characterisation. The company invests significantly in R&D and applications development, and provides detailed know-how to support its range of products. Expert teams guide and support users around the world in addressing their individual powder challenges, focusing on delivering the most relevant information for the process. The result is world-leading solutions for understanding powder behaviour - in development, formulation, scale-up, processing, quality control, or anywhere that powders have a role.
Freeman Technology’s solutions include the FT4 Powder Rheometer®, a uniquely universal powder tester, and the Uniaxial Powder Tester, a complementary tool for quick and robust powder assessment. Systems are installed around the world in the chemical, pharmaceutical, toners, foods, powder coatings, metals, ceramics, cosmetics, and many other industries. They deliver data that maximise process and product understanding, accelerating R&D and formulation towards successful commercialisation, and supporting the long term optimisation of powder processes.
Freeman Technology is also the global distributor for Lenterra sensor instrumentation which provides in-line, real-time flow measurement solutions to enhance process understanding, and improve manufacturing efficiency and quality.
Founded in 1989 as a developer of automated testing systems for materials characterisation, the company has focused exclusively on powders since the late 1990s and in 2018 became part of Micromeritics Instrument Corporation The company’s R&D, manufacturing and commercial headquarters are in Gloucestershire, UK, with operations and distribution partners in key global territories.
In 2007 the company received the Queen’s Award for Enterprise in Innovation and in 2012 the Queen’s Award for Enterprise in International Trade.
Sponsored Content Policy: News-Medical.net publishes articles and related content that may be derived from sources where we have existing commercial relationships, provided such content adds value to the core editorial ethos of News-Medical.Net which is to educate and inform site visitors interested in medical research, science, medical devices and treatments.