With the recent update to EU GMP Annex 1, it is necessary to assess existing practices to confirm that the monitoring system installed, selected to meet the Annex 1 requirements, complies. This article will examine the Annex 1 requirements in conjunction with the current systems being put in place.1
Cleanroom classification
In the pharmaceutical industry, cleanrooms are categorized based on the level of airborne particle concentration necessary to meet the cleanliness standards required for the specific manufacturing process.
Determining the cleanroom class relies on valid statistical measurements and the operational status of the room’s filtration and equipment. Essentially, it involves calibrating the room to ensure it aligns with its intended classification rather than primarily considering the risk of application.2
Three phases are involved in particle counting within cleanrooms:
- As Built: A completed room with all services connected and operational but without production equipment or personnel.
- At Rest: All services are connected, equipment is installed and functioning as agreed, but no personnel are present.
- Operational: All equipment is installed and operating as specified, and a defined number of personnel are present, following established procedures.
The airborne particle count test involves counting particles at specific grid locations within the cleanroom. These test points should be evenly distributed throughout the room and at a working height to demonstrate the air cleanliness quality in the work area.
Pharmaceutical cleanrooms typically operate within Class 5 (most aseptic areas), Class 7 (surrounding areas), or Class 8 (support areas). Refer to Figure 1 for a visual representation.
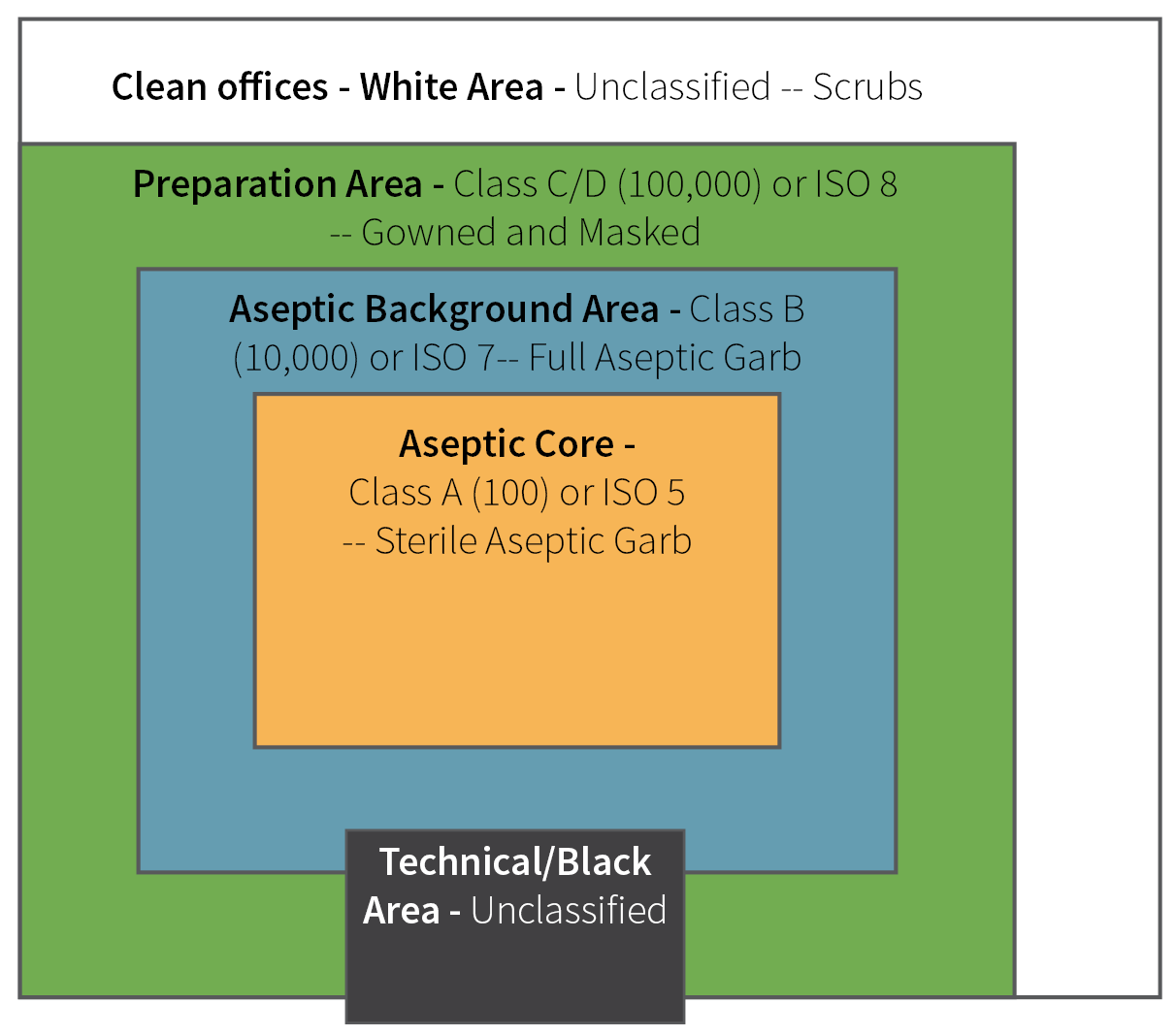
Figure 1. Diagram of typical ISO rating in areas of cleanroom. Image Credit: Particle Measuring Systems
Pharmaceutical cleanroom utilization
After a cleanroom undergoes testing to confirm its compliance with cleanroom classification standards, typically using a Light Scattering Aerosol Particle Counter (LSAPC), the achieved classification determines the allowable production activities within that cleanroom or clean air device. The FDA identifies two distinct zones:
- Critical Areas contain products that could become contaminated if exposed and are designated as Grade A (ISO5) in the Annex 1 document. Maintaining product safety requires strict control and consistent quality in the environment where aseptic operations take place.
- Supporting Clean Areas are designated as grade B/C/D within Annex 1 and are used for activities outside the critical core. These areas generally pose a lower risk of contaminating the finished product.
Once a cleanroom or clean air device proves its cleanliness certification, it must also demonstrate the ability to maintain control throughout production.
The environment should undergo rigorous monitoring to ensure ongoing awareness of current conditions, even detecting occasional events that could have serious consequences if overlooked.
Continuous monitoring generates a substantial amount of data, which is used to spot trends.
The manufacturing facility should establish a comprehensive environmental monitoring program. This program covers monitoring for both nonviable and viable airborne particles, surface-based viable contamination, and, in aseptic areas, personnel.
The program outlines monitoring frequencies and locations for sampling points, sets warning and alarm thresholds for each area, and specifies corrective actions in case any area deviates from expected results.
When limits are exceeded, actions should include an investigation into the source of the issue, an assessment of its potential impact on the product, and implementation of measures to prevent a recurrence.
Contamination control strategy
The Contamination Control Strategy (CCS) comprises the environmental monitoring program and must be applied throughout the facility. This strategy needs to define critical control points as part of a risk assessment and evaluate the effectiveness of controls and monitoring methods utilized to manage contamination-related risks.
The CCS should undergo regular review, particularly in the initial implementation stages, and it should be updated to promote ongoing enhancement of monitoring and control techniques, ultimately improving overall process quality.
Key elements to consider in a Contamination Control Strategy include:
- Design of the plant and processes
- Premises and equipment
- Personnel
- Utilities
- Raw material controls
- Product containers and closures
- Vendor approval—key suppliers
- Outsourced services, such as sterilization, ensure the process is operating correctly
- Process risk assessment
- Process validation
- Preventative maintenance
- Cleaning and disinfection
- Monitoring systems—the introduction of scientifically sound, modern methods that optimize the detection of environmental contamination
- Prevention—trending, investigation, corrective, and preventive actions (CAPA)
The Facility Monitoring System’s scope should encompass items listed as (i, ii, iii, ix, x, xii, xiii, and xiv). Many of the CCS considerations should be integrated into the Environment Monitoring (EM) program.
Environmental monitoring requirements
Table 1. EU GMP Annex 1 room classification table (Annex 1 2022). Source: Particle Measuring Systems
EU GMP Grade |
At Rest |
In Operation |
Maximum number of particles permitted/m3 equal to or greater than the tabulated size |
0.5 μm |
5.0 μm |
0.5 μm |
5.0 μm |
A |
3520 |
Not Specified(a) |
3520 |
Not Specified(a) |
B |
3520 |
Not Specified(a) |
352,000 |
2930 |
C |
352,000 |
2,930 |
3,520,000 |
29,300 |
D |
3,520,000 |
29,300 |
Not Predetermined(b) |
Not Predetermined(b) |

Figure 2. Footnotes to above table in annex 1 2022. Image Credit: Particle Measuring Systems
Monitoring should employ appropriate techniques aligned with the Risk Assessment. For many monitoring needs in lower classification areas, a portable instrument may suffice.
However, the grade A area must maintain continuous monitoring (for particles ≥ 0.5 and ≥ 5 µm) with a suitable sample flow rate (at least 28.3 LPM / 1 CFM) to capture all interventions, transient events, and system deterioration.
The system should frequently correlate each sample result with alert levels and action limits to promptly identify and address potential excursions.
Alarms should sound if alert levels are exceeded. Procedures should specify actions in response to alarms, including potential additional microbial monitoring.
Continuous monitoring within Grade A is achieved using point-of-use dedicated sensors connected to central monitoring software, which can send alarms to cleanroom operators or relevant groups. These alert and alarm occurrences are permanently recorded in the system’s audit trail.
Determining the sample point(s) location is a vital aspect of the system. These locations should be identified following a documented Environmental Monitoring Risk Assessment (EMRA) and include the following information:
- Sampling locations
- Frequency of monitoring
- Monitoring method used
- Incubation conditions (e.g. time, temperature(s), aerobic and/or anaerobic conditions)
It should be based on the following inputs from the site:
- Detailed knowledge of the process inputs and final product
- Facility
- equipment
- Specific processes
- The operations involved
- Historical monitoring data
- Monitoring data obtained during qualification
- Knowledge of typical microbial flora isolated from the environment
- Air visualization studies should also be included
Suitable sample point locations are also impeded by:
- Physical installation of sample probe
- Physical installation of instrument
- Tubing length, bends, and bends radii between the two
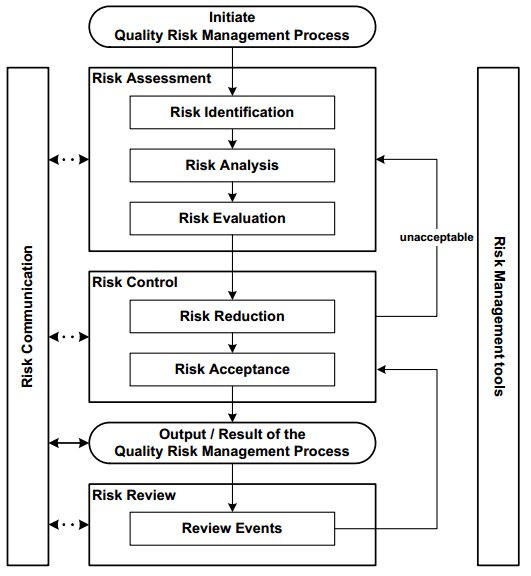
Figure 3. Steps for risk identification and analysis. Image Credit: Particle Measuring Systems
Typical automated continuous monitoring system
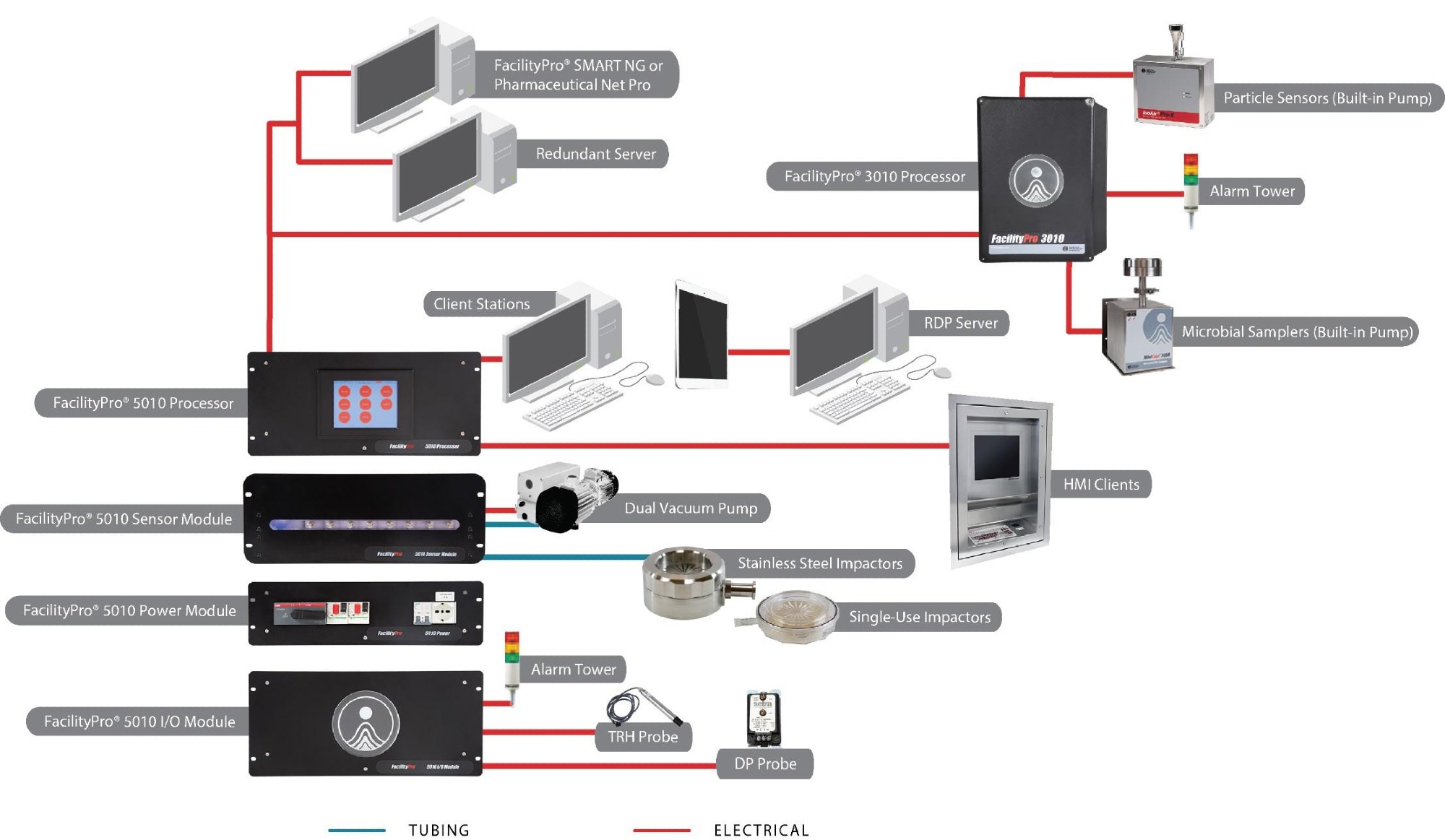
Figure 4. Example facility monitoring system (FMS) Setup. Image Credit: Particle Measuring Systems
The instrumentation employed in creating an integrated solution generally includes the following components:
- Particle counting: To ensure continuous data collection, a dedicated sensor is stationed at each location and operates continuously during both the set-up and production phases of manufacturing.
The sensor(s) transmit data to a central processing unit, responsible for handling response processing, data buffering, and sensor controls. The sensor can either have an internal pump or be connected to a remote vacuum source, both of which are managed through the central interface within the software application.
- Microbial sampling: In situations where the need for total particle counting is identified, microbial sampling becomes a requirement. The sampling head is placed within the environment to ensure that any exhaust is controlled by the system and not released locally within the critical space.
Microbial samplers are devices with fixed flow rates (typically 25 LPM), and this flow control can be managed either locally (using a dedicated device) or centrally (using the same central vacuum source as the particle counter sensor sub-system). Start and stop controls are executed via the software interface.
- Alarm beacons: These supplementary devices enable local notification through both visible and audible signals, alerting operators within the controlled space if a system falls out of tolerance. For enhanced information, a remote interface can be positioned within the operator’s field of view, and if located within the clean core of the facility, it can also be interactive.
- Central software system: The system is structured with Industrial Automation architecture, featuring a central processing system responsible for gathering data from field sensors and controlling remote devices while communicating with a SCADA (Supervisory Control and Data Acquisition) software package. The following functionalities should be accessible to interact effectively with the system and generate data reports.
- Data and status information displays - The main page serves to present the facility layout along with the current data and status info for each sampling point. It is also possible to view data, status, and sampling details for individual dedicated areas all on one screen.
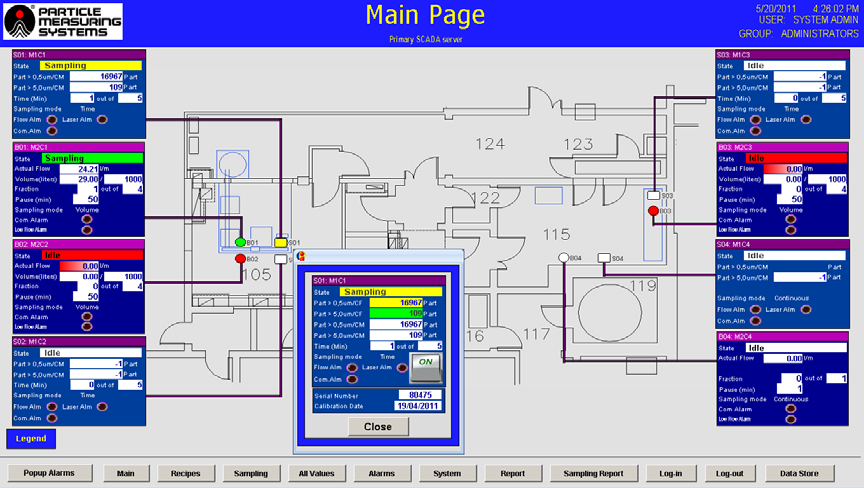
Figure 5. Main page of facility monitoring software. Image Credit: Particle Measuring Systems
- User and area segregation - In compliance with CFR 21 Part 11 and Annex 11, control and management of single-user access is vital to ensure that each person adheres to the user’s Standard Operating Procedures and aligns with their role, responsibilities, and training.
The SCADA software should also guarantee the proper separation of data when multiple departments are connected and supervised by the same system.
- Report generator - The SCADA software must have a report generator that can create easily readable reports for all recorded data, including audit trails (events), data/statistical summaries, and trend charts. The system should be able to retrieve historical data as defined in the site’s User Requirement Specification for the associated system.
With data filters for categories such as date, time, location, and batch, accessing data should be straightforward, and when necessary, it can be exported or printed to support product release.
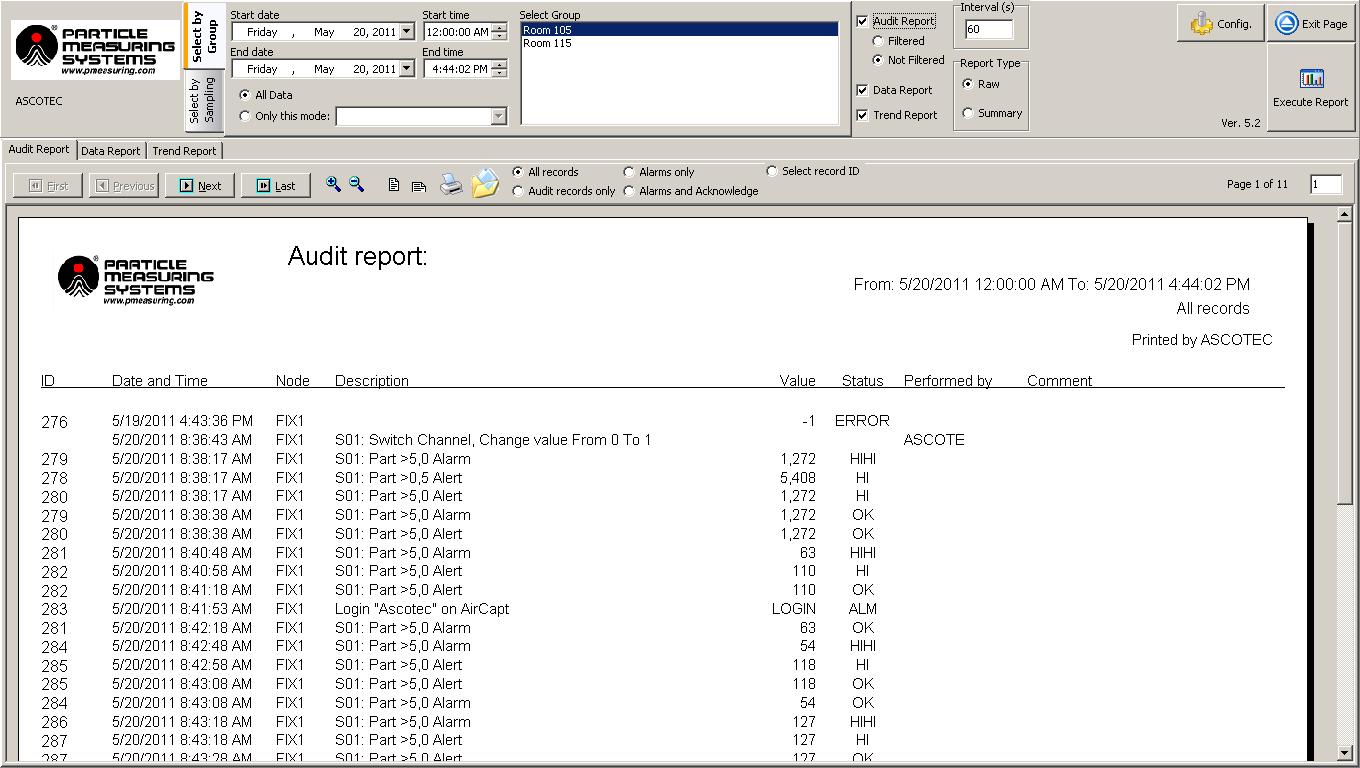
Figure 6. Report generator. Image Credit: Particle Measuring Systems
- Alarms - The alarm display provides essential information such as date, time, area, description, and value for alarms. It also includes a feature for acknowledging alarms, and the display allows users to sort alarms using various criteria. Determining the alarm set point within the software is based on the limits table in Annex 1 and historical data for each sampling location.
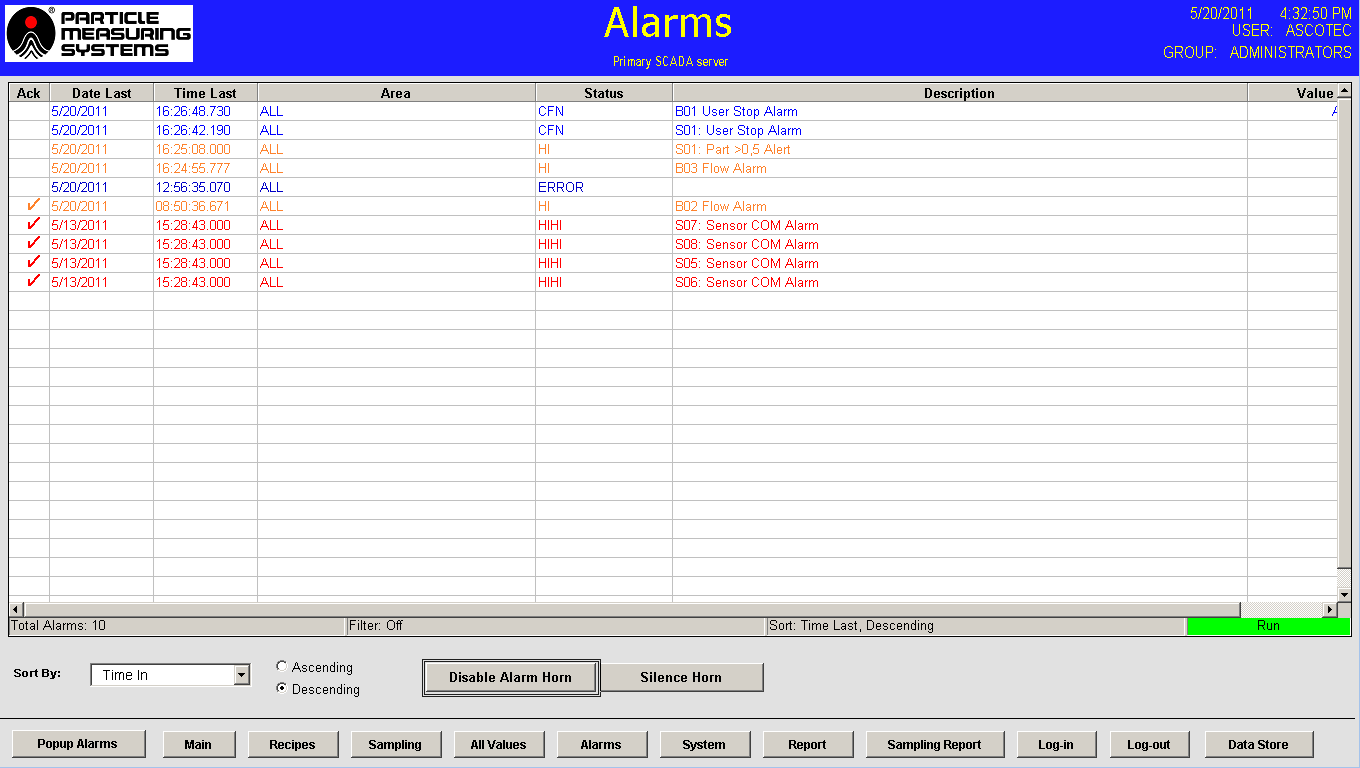
Figure 7. Alarms page. Image Credit: Particle Measuring Systems
Annex 1 (2022) also notes in Section 9, that
“The occasional indication of macro particle counts, especially ≥ 5 µm, within Grade A may be considered to be false counts due to electronic noise, stray light, coincidence loss, etc. However, consecutive or regular counting of low levels may be indicative of a possible contamination event and should be investigated. Such events may indicate early failure of the room air supply filtration system, equipment failure, or may also be diagnostic of poor practices during machine set-up and routine operation.”
Therefore, when considering the reason for setting alarms, it is important to take into account both the frequency of events and not just their magnitude. These factors should be integrated within the CCS.
Further insights and alerting methods can also be discovered in ISO 14644-2:2015, in section B.3.1. Environmental Monitoring Systems should be capable of easily and reliably configuring an “N of M” strategy to ensure that out-of-specification events are escalated to alarms when the specified conditions are met.
Like all integrated systems, especially those utilizing a central software package, validation plays a significant role in the timeline of any installed project.
The assessment and distribution of documents might take several weeks, particularly when multiple departments are involved. It is essential to discuss the overall project duration with the installation project team to ensure it aligns with the site’s requirements for shutdown accessibility.
Conclusion
The monitoring of pharmaceutical aseptic production environments has a well-established foundation, and the changes introduced in the updated Annex 1 (2022) do not significantly alter the monitoring requirements.
The formal risk assessment and the inclusion of data within a CCS constitute a more comprehensive addition to the continuous systems established following previous regulations.
This emphasis primarily enhances the documentation requirements, deviating from the traditional expectations of a continuous system.
Acknowledgments
Originally authored by Mark Hallworth from Particle Measuring Systems.
References
- European Commission. The Rules Governing Medicinal Products in the European Union Volume 4 EU Guidelines for Good Manufacturing Practice for Medicinal Products for Human and Veterinary Use: Annex 1, Manufacture of Sterile Medicinal Products, Annex 1 (2022).
- International Standards Organization. Cleanrooms and associated controlled environments — Part 1: Classification of air cleanliness by particle concentration, ISO Standard No. 14644-1:2015 (2015).
About Particle Measuring Systems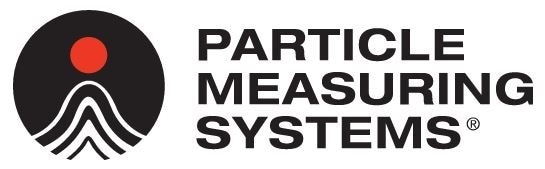
Particle Measuring Systems has 35 years experience designing, manufacturing, and servicing microcontamination monitoring instrumentation and software used for detecting particles in air, liquid, and gas stream as well as molecular contamination monitoring.
Specific applications include cleanroom monitoring, parenteral sampling, filter and in-line testing in deionized water and process chemicals, and point-of-use monitoring of inert gases and in-situ particle monitoring. Specialty monitoring includes parts cleanliness testing with a highly automated solution.
Particle measuring systems
Whether you want to protect product or meet industry requirements, such as ISO 14644, USP 797, or GMP, Particle Measuring Systems has a large variety of particle counters and molecular monitors to meet your needs. With 35 years experience, we have the proven reliability to support your application.
Particle counters
Protect your product with our reliable particle counters. We have airborne, portable, and liquid particle counters for a wide variety of applications including DI water, chemicals, and cleanroom monitoring. Compare particle counters or learn how to monitor your cleanroom or product by reading our papers.
Molecular contamination monitors
Molecular contamination creates costly problems to high value products, production processes, and equipment surfaces. We have solutions for both Airborne Molecular contamination (AMC) and Surface Molecular contamination (SMC). With parts-per-trillion limits of detection, real-time sampling, NIST traceable calibrations, and various data analysis packages, you can monitor in confidence.
Gas detectors
If you need gas detectors for process control or continuous emissions monitoring, we can help. Get real-time, reliable results with our ammonia, hydrogen fluoride, and chlorine detectors for worker protections, CEMs, and pollution monitoring.
Sponsored Content Policy: News-Medical.net publishes articles and related content that may be derived from sources where we have existing commercial relationships, provided such content adds value to the core editorial ethos of News-Medical.Net which is to educate and inform site visitors interested in medical research, science, medical devices and treatments.