Granulation is important in the pharmaceutical industry because of increased pressures due to the costs of manufacturing solid dosage forms. Granulation forms coarser collections from fine powder. Collections contain fixed, dry grains, each of which is an assortment of powder particles of adequate strength. Granules can be used as pharmaceuticals or as a transition in manufacturing capsules or tablets.
Focusing on technical expertise, Executive Director Technology Thorsten Wesselmann said, “With one of the largest range of different granulation processes on the market, we offer our customers the right system for every process.”
Stressing L.B. Bohle’s extraordinary position, Wesselman commented, “We can therefore supply both standard systems and customized solutions for batch and continuous processes.”
Compact module
Bohle combines the independent components of the GMA high shear granulator, BTS wet sieve, BFS Bohle fluid bed system, Bohle Uni Cone BUC®, cyclone separator, and BTS dry sieve into an efficient plant. This allows the processing, control, cleaning, zone concept, explosion protection, and qualification to be synchronized with each other.
The compact module offers a space-saving design with the individual components installed beside each other. The direct transfer of the product from the GMA’s outlet valve to the BFS suction valve is done through a stainless steel pipe that can integrate the extremely reliable tangential sieve. An extra drain valve has been installed in the BFS process tank eliminating the need to modify the transfer and drain lines during the process.
Thorsten Wesselmann explains, “In our opinion, the compact system is an effective solution when it comes to optimizing classic wet granulation in an economical and ergonomic way. The compact system sets new industry standards due to its many technological advances and logical safety concept.”
Advantages:
- High shear granulator GMA and BFS fluid bed dryer are installed next to each other in the wall
- Minimal space and installation height required
- Multiple uses for various processes
- A single control panel for both machines
- WIP guarantees quick cleaning times
- High quality
Fluid Bed granulation
Fluid bed systems have been utilized for decades in the pharmaceutical industry. The addition of a wet or alcoholic granulation medium compacts the mix of dry powder particles. The fluid has a volatile solvent that is eliminated with drying.
Mr. Wesselmann said, “For a long time, fluid bed solutions were dominated by top-spray systems. However, the benefits of systems with tangential spray nozzles are becoming more and more apparent and these systems are now tending to take over from top-spray granulators.”
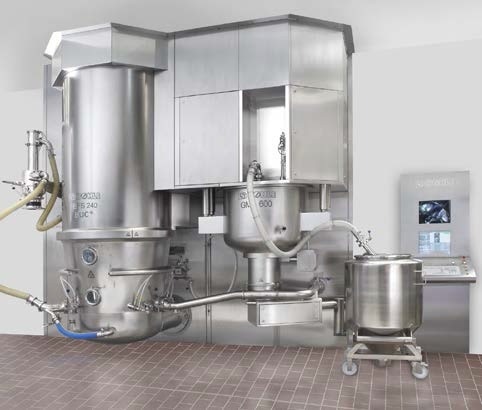
Figure 1. The compact unit with the BFS fluid bed system and the patented Bohle Uni Cone BUC® process sets new standards. Image Credit: L.B. Bohle Maschinen und Verfahren GmbH
Granules move tangentially with lower fluid heights and do not need a high-volume increase. The installation height requirements are reduced saving production space and costs.
In Thorsten Wesselmann’s opinion, a benefit of the tangential design in plants from L.B. Bohle is “that granulation, coating and drying can be carried out in a single system without altering the equipment setup.”
L.B. Bohle designed the BFS fluid bed system with tangentially mounted spray nozzles and the patented Bohle Uni Cone BUC®, a precisely positioned air distributor plate with a conical displacement cone for volumes of 1 to 500 kg. Its pressure shock resistance of up to 12 bars makes the BFS the perfect choice for organic processes.
Extra savings in manufacturing time and cost are available with effective cleaning methods and shortened transfer times of products. The symmetrical structure streamlines scaling up. A new, sheltered multi-purpose valve located immediately above the distributor plate enables dust-free suctioning and draining of the product container.
For Wesselmann the “clear benefits with regards to ergonomics and cleaning that make the BFS stand out significantly from other fluid bed systems on the market.”
Single-Pot granulation
Single-Pot granulation has been utilized for decades by the pharmaceutical industry. The VMA granulator accomplishes the high shear wet granulation, mixing, and drying (vacuum drying, microwave heat drying, or carrier-gas drying) in one container.
Single-Pot granulators offer the following benefits:
- Secure manufacturing inside a closed container in a vacuum
- Extremely efficient mixing and granulation (including low doses of active agents < 1%)
- Low drying temperatures
- Quick, easy cleaning and fast product changeover for small product contact surfaces
- Efficient recovery of solvents with cooling water
- Compact footprint requiring less space
The VMA single-pot granulator product range offers classic mixer granulators with agitator and chopper units, and a top drive system. Two stirrers create shearing and loosening of the product. This prevents clumping and guarantees the granule produced is optimal.
Mr. Wesselmann states that the GMP-compliant process bowl with double jacket is “the heart of the VMA.”
The main units are installed inside the granulation pot’s lid (Top-Drive). The process tank is emptied into a container through a cone-shaped sieve (BTS 200) in the floor outlet (IBC). Formula-controlled cleaning is automatic. The VMA produces batch sizes from 20 to 960 liters (about 256.61 gals) and can potentially be used in explosive environments.
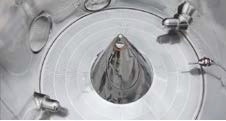
Figure 2. The Bohle Uni Cone BUC® is a specially slotted air distributor plate with a conical displacement cone. The design allows for completely fluidized particles. Image Credit: L.B. Bohle Maschinen und Verfahren GmbH
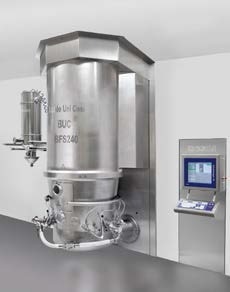
Figure 3. The Bohle fluid bed system is a multi-purpose system for drying, granulating and coating and offers numerous advantages over systems in the top spray or bottom spray process. Image Credit: L.B. Bohle Maschinen und Verfahren GmbH
High-shear granulation
High-shear granulation adds a binding fluid to the powdeed particles in a closed tank equipped with an agitator blade and chopper. Using high shear and compaction, the agitator blade reliably provides consistent granulation. The formation of dense granules is resolved by the chopper, which prevents extreme granulate growth and disperses the granulation medium throughout the product.
The advantages:
- Low fluid requirements
- Simplified unloading
- Closed system
- Granulation control by time, quantity, or output
- Easy cleaning and the water drains completely
Twin-screw granulation
Twin-screw granulation (TSG) is a recognized technique for continuous wet granulation and is the beginning point for companies considering continuous production of pharmaceuticals.
The powder selected for granulation is fed onto two screws that turn in the same direction inside a cylinder. The screws move the powder through the processing area while kneading and mixing it simultaneously.
This TSG design has numerous benefits:
- Material in the process has short rest times (< 1 minute – a few seconds)
- Quick and efficient response to deviations in process and quality
- Less space is needed for the machines and associated GMP areas required
- Mixing and granulation is completed in one step in the least amount of time possible
- Instruments were introduced to provide 100% in-line quality control. Rejection of entire batches is no longer required, and the ability to selectively eject inferior quality products is no longer required.
- Experimental test plans can be implemented quickly
Thorsten Wesselmann describes the system’s potential: “Due to the flexibility and simple implementation of the process, the TSG is the perfect, versatile machine for continuous manufacturing processes in research and development and in production.”
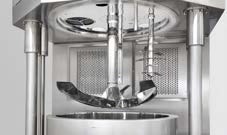
Figure 4. A binding fluid is added to the powdery particles in the high-shear granulator. The agitator blade guarantees effective granulation. Image Credit: L.B. Bohle Maschinen und Verfahren GmbH
Roller Compaction
Roller Compaction is an accepted method in the pharmaceutical industry used for a variety of products, including moisture and temperature-sensitive materials. In comparison to wet granulation, energy-intensive drying techniques are not required. This reduces the size of investment required for equipment and production facilities. Reducing energy consumption results in a lower cost per batch. If the need for drying is eliminated, then stocking, extracting, and disposing of solvents is unnecessary.
Roller compactors provide a compacting process with exceptionally high material throughput. A single machine can produce a variety of products and batch sizes.
Highlighting Bohle’s benefits, Mr. Wesselmann said, “L.B. Bohle’s BRC series combines a high level of product capacity with minimum material loss. This system outclasses rival solutions by generating force through purely electromechanical means to ensure consistent ribbon properties.”
The innovative BRC controls compacting force and ribbon thickness, producing an even distribution of material over a production range of <1 - 400 kg/h (about 885.81 lbs.). The advanced system design eases handling and reduces the assembly process. The hygienic design with standard integrated washer nozzles provides an efficient WIP process.
The cone-shaped Bohle Turbo Sieve BTS and sieve inserts can easily reduce the ribbons into granules for the required particle size dispersal even for high material throughputs. For Thorsten Wesselmann, this is a benefit “that each BRC can be mounted with a different rotary sieve within minutes to adjust to new process and ribbon requirements.”
The practical GMP-compliant design and PAT tool support allows the compactor to meet the needs of pharmaceutical “Quality by Design.”
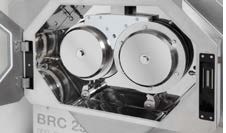
Figure 5. The BRC series guarantees extremely consistent ribbon properties by generating force through purely electromechanical means. Image Credit: L.B. Bohle Maschinen und Verfahren GmbH
About L.B. Bohle Maschinen und Verfahren GmbH
L.B. Bohle with the headquarter in Germany, is one of the largest system suppliers for the pharmaceutical processing industry and related sectors. Internationally active, they focus on machinery and equipment as well as process technology and components.
In addition, L.B. Bohle offer sustainable solutions for demanding production processes in batch and continuous manufacturing for the oral solid dosage production. For instance, L.B. Bohle provides single or interlinked machines for the processes Weighing, Dry and Wet Granulation, Grinding and Sieving, Container Blending, Tablet Coating and Tablet Handling.
Sponsored Content Policy: News-Medical.net publishes articles and related content that may be derived from sources where we have existing commercial relationships, provided such content adds value to the core editorial ethos of News-Medical.Net which is to educate and inform site visitors interested in medical research, science, medical devices and treatments.