The 208HRD High Resolution Sputter Coater from Cressington provides real solutions to the issues faced while coating hard samples for FESEM imaging.
Extremely thin, fine-grained, and uniform coatings are required by FESEM applications to remove charging and enhance contrast on low-density materials. To reduce the effects of grain size, the 208HR provides a complete range of coating materials and provides unparalleled control over thickness and deposition conditions.
An extensive range of operating pressures have been provided by the 208HRD Turbo Pumped High Vacuum System, enabling accurate control of both uniformity and conformity of the coating, reducing charging effects.
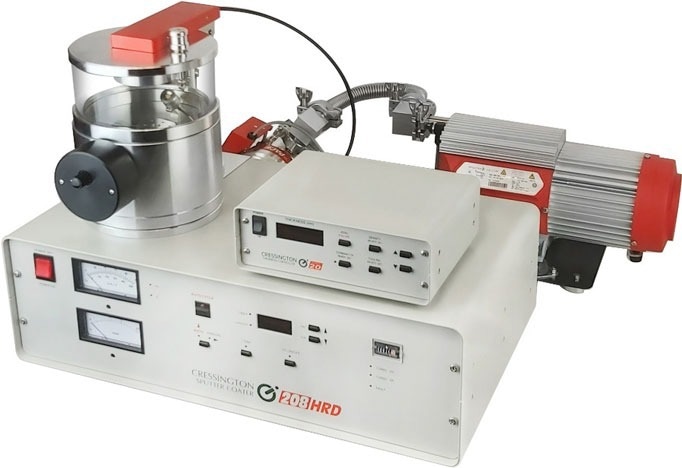
208HRD shown above with Rotary-Planetary-Tilting RPT Stage and MTM-20 Thickness Controller. Image Credit: Ted Pella, Inc
The 208HRD High Resolution Sputter Coater is an entire coating solution, such as standard:
- Pumping system comes with turbo pump, backing pump for turbo, and vacuum connections
- Rotary-Planetary-Tilting Stage with sample holder selection
- MTM-20 High Resolution Film Thickness Controller
- Target selection like Pt/Pd, Ir, or Cr. See here for a full list of targets.
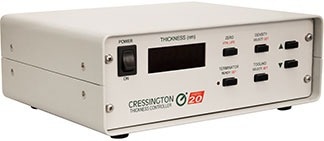
MTM-20 High Resolution Thickness Controller. Image Credit: Ted Pella, Inc
The 9524 Rotary-Planetary-Tilting RPT Stage Shown with optional MTM Crystal Monitor from Ted Pella, Inc.
Rotary-Planetary-Tilting RPT Stage demonstrating variable speed settings and adjustable tilt. Video Credit: Ted Pella, Inc
Main features
Wide choice of coating materials
The availability of magnetron head design and effective gas handling enables an extensive choice of target materials.
Economical target utilization
The 208HRD provides a smaller diameter target and altered chamber configurations to offer highly economical usage for expensive materials like iridium.
Precision thickness control
Thickness improved for FESEM application using the MTM-20 High Resolution Thickness Controller, which consists of a resolution of 0.1 nm. This allows accurate and reproducible thin coatings, particularly in the 0.5 to 3 nm range, a thickness preferred for FESEM applications.
Multi-angle stage movements
Separate rotary, planetary, and tilting stage movements guarantee even coating with outstanding conformity, even on highly topographic samples. Around four sample holders are offered with options to house sample sizes as large as 32 mm in diameter.
Variable chamber geometry
Chamber geometry is utilized to adjust the deposition rate to maximize the structure. Height can be adjusted by adding metal spacer rings (2 included).
Compact, modern, benchtop design
Space and energy-saving design removes the requirement for floor space, water, or specialized electrical connections. Combined turbo pump guarantees fast pump down and high positive pumping speed during the sputtering process. Integrated turbo pump guarantees quick pump down speed. The backing pump for the turbo is known as a diaphragm pump, thereby offering oil-free operation.
208HRD sputter head
The 208HRD uses a small 28mm diameter target design that provides greater efficiency to better use highly-priced target materials like iridium. An extra advantage of using a smaller diameter sputter source is that it aids in lowering the entire system cost with the target compared to larger target systems.
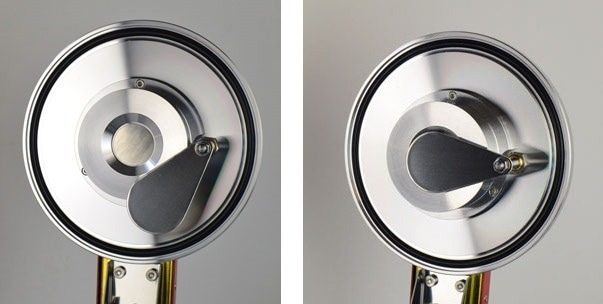
28 mm Diameter Target. Image Credit: Ted Pella, Inc
Preferred coating materials for FESEM applications:
- Ir: Outstanding and very fine-grain coating material
- Cr: Excellent for semiconductor materials and high-resolution back-scattered electron imaging
- Pt/Pd: General-purpose high-resolution coating material available for non-conducting specimens
208HRD Chamber
The 208HRD consists of a modular chamber including a glass chamber, rotary-planetary-tilting stage, and metal spacer rings (2 included). Such components are labeled in the image below.
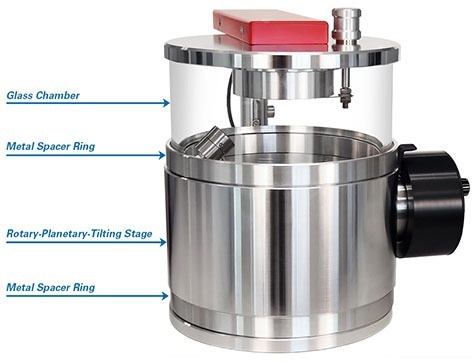
208HRD Chamber as shown on 208HRD. Image Credit: Ted Pella, Inc
The sputter head support pillar could be adjusted into three positions, altering the entire chamber height. Every adjustment location refers to a different metal spacer, glass chamber/rotary-planetary-tilting RPT stage configuration.
The addition of a spacer ring present above the RPT stage raises the deposition distances by 15 mm (height of metal spacer ring). Two metal spacers have been included with the 208HRD, but a third (#8091-1) could be purchased individually.
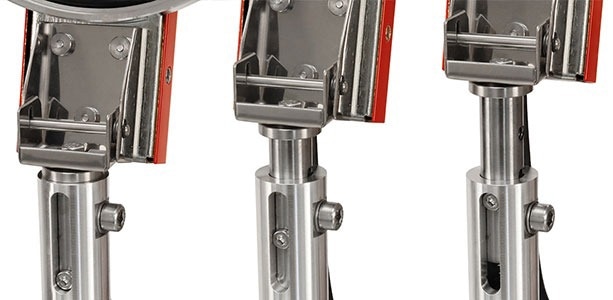
Support pillar adjustment locations. Image Credit: Ted Pella, Inc

Chamber configuration variations. Image Credit: Ted Pella, Inc
Optional items
Also, a Second Chamber Outfit (#7021-208HR) is available, consisting of a stationary stage with a 150 mm tall chamber and an extra spacer ring.
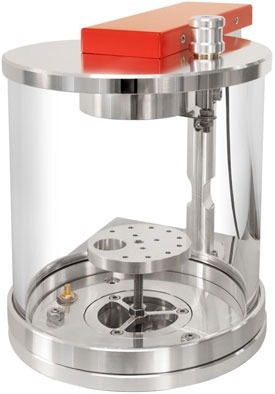
Stationary stage with tall glass chamber. Image Credit: Ted Pella, Inc
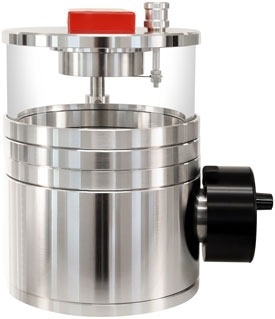
Rotary-Planetary-Tilting stage with third spacer ring. Image Credit: Ted Pella, Inc