Through the years, a variety of pump technologies have been utilized or measured for the use of virus filtration, chromatography, and TFF unit operation processes. Two of these that are the most frequently used in biopharmaceutical manufacturing are peristaltic and lobe pumps.
It is important to note however that each of these has been discovered to have inefficiencies in their operations that may make them incompatible when utilized in the methods outlined above.
Lobe Pumps
As most biopharmaceutical materials are held within a low-viscosity aqueous solution, lobe pumps may not be efficient due to slippage occurring when they operate. The slips are variable, between 10% and 100%, and this is according to the back pressure in each system.
Slippage can also cause a greater amount of shear damage and makes the method less energy efficient. If this is utilized in a recirculation loop over a large amount of time, such as in a TFF filtration system, additional investments are needed to keep the system cool as more heat is added to the product in order to avoid overheating.
Mechanical seals are also present in lobe pumps. These can lead to a controlled product leak and cannot give full containment unless unique (and more costly) seals, and seal barriers are utilized.
The sterility needed for the preparation of biopharmaceuticals also means that external contaminants cannot be introduced into the process of purification. This is a factor that pumps with mechanical seals cannot fully ensure.
Moreover, the contact needed between the internal compartments in the lobe pump can result in wear and tear, along with the production of particles that can mean increased contamination of the product.
Solid particulates, for example, undissolved crystals of salt, can create intense damage to the lobes. This also leads to damage to the whole manufacturing yield. Lobe pumps are therefore more costly to function due to more power being necessary to reduce the chances of pump slippage.
Peristaltic (Hose) Pumps
The most common detriment in the use of peristaltic pumps is also their most obvious feature. Their operation method will likely create pulsation, and as detailed in the most common features of unit operation, pulsation always creates challenges in the manufacture of biopharmaceuticals.
Peristaltic pumps also have a lesser amount of flow and pressure-handling capabilities. As an example, they are unable to consistently produce the greater discharge pressures (for example 4 bar, or 58 psi) that are needed in certain fluid-handling processes.
These types of pumps can also produce a small amount of material from the hose. This is a feature called ‘spalling’ where hose material contaminates the pumped product which means there is a lesser amount of purity.
In the event of spalled material from the hose contaminating the filter, this can foul the filter and make the overall process less efficient.
Moreover, the contamination of the filter can cause variations in flow rate because the hose can become mechanically deformed during the pumping process. Overall, the main issues with utilizing lobe and peristaltic pumps in unit operations are as follows:
- Shear is frequently a feature in lobe pumps, and if this is present it can cause damage to the pumped material
- If pulsation is present, which is certain to be found in peristaltic pumps, the flow will be inconsistent which leads to inaccuracies in the outcome
The Solution
The quaternary diaphragm pump is a beneficial solution to the adverse effects of lobe and peristaltic pumps.
The inspiration behind the creation of the quaternary diaphragm pump goes back 30 years to the middle of the 1980s. This is what is now commonly called ‘the birth of the modern biotech industry.’
In the year of 1986, Frank Glabiszewski, an engineer for a German filter manufacturer, was becoming more and more irritated by the operation of the pumping technologies that were frequently used in the applications of chromatography and TFF.
We were using peristaltic pumps but we found out that these pumps were not made for TFF applications. We were checking the marketplace looking for better pumps and spent 80% of our time looking for pumps."
Frank Glabiszewski, Engineer, A German Filter Manufacturer.
Glabiszewski continued, “One night I went home and I was sitting in my car frustrated after a pump failure and asked myself a question, ‘Which type of pump did Mother Nature invent to process sensitive biologic fluids like blood?’”1
The obvious solution to this question was the human heart. With this image in mind, Glabiszewski touched base with his friend and partner in engineering, Josef Zitron, to design and realize the operation of the quaternary diaphragm pump technology.
This new technology was eventually realized in the year 2000, which followed the pair’s founding of a company that would begin to produce quaternary diaphragm pumps for utilization in biopharmaceutical manufacture.
The pair’s creation has increased in usage over the past 15 years, and technological developments have arisen with its rise in popularity. It was modified with the use of disposable plastic heads, along with the use of wetted parts, to make it useful in the up-and-coming biopharmaceutical production market.
The operating means of the quaternary diaphragm pump bears the closest likeness to the operation of the human heart. Its four-piston diaphragm technology allows for soft, rhythmic pumping actions similar to heartbeats.
This operating action also creates four pumping strokes of the pistons that function at the same time, which effectively lessen pulsation because each pulse of the four diaphragms are produced by a unique shaft that is fixed to an electric motor.
The process of operation in the quaternary diaphragm pump enables it to softly, reliably, and securely, produce low viscosity aqueous solutions and biopharmaceutical materials that are particularly sensitive to shear forces and pulsation as they are pumped.
As no mechanical seals or wetted rotating parts are necessary due to the four-piston design of the pump, product containment is guaranteed with the chances of damage or particulate generation being reduced.
The method of operation within the quaternary diaphragm pump also creates free from risk, dry-running, and self-priming features with a high ratio of turndown. Pump technology with a high ratio of turndown means that a wide flow range is created. This makes the pump easy to use in a varied range of applications.
In regards to particular unit operations, quaternary diaphragm pumps can be utilized to pack chromatography columns and then pump biopharmaceutical material through the column. These are important features that necessitate a low amount of pulsation, with consistent and reliable flow pressures and rates.
In the applications of TFF, these pumps also create the consistent control of flow rates that are critical in creating the most beneficial yields of filtrate.
As today’s biopharmaceutical manufacturing processes are constantly changing, these pumps are quickly becoming the preferred technology for utilization in single-use production setups which are used more frequently in the current climate.
In short, a single-use pump allows biopharmaceutical manufacturers to reduce cleaning costs and pump validation, by utilizing a pump with a replaceable head. The outcome of this means that the purity and cleanliness of the product are both protected, while also reducing the chances of cross-batch or product contamination.
Listed below are the other benefits of utilizing quaternary diaphragm single-use pumps:
- Utilized for one product, or in a single production campaign
- At the end of the production campaign, the pump chamber that has been in contact with the fluids can be disposed
- Can be utilized for a particular amount of time before wetted parts are replaced, which reduces the costs of maintenance
- Where a stainless-steel pump is necessary for the operator, the plastic pumping chamber is replaceable with a stainless-steel alternative
- If a pump failure happens, the replaceable nature of the chamber means it can be easily replaced in less than five minutes
- Used when cleaning in place (CIP) or steam sterilization is not practical or possible.This means that they are more simple and reduce the costs of the overall process, as it eliminates the use of contaminated cleaning chemicals or water solutions that need to be disposed of or treated.
The treatment and disposal of cleaning fluids detailed above can alone be an important factor when considering single-use alternatives.
It is worth noting that not all pump technologies are wholly compatible with every feature of each fluid-handling application. In these examples, the design and operation of the quaternary diaphragm pump reduces it to handling fluids that have a maximum viscosity of 1,000 centipoise (cPs) and that have particulates up to 0.1 millimeter in diameter.
Conclusion
As biopharmaceutical products have a critical use, it is important that unit operations are in line with strict manufacturing guidelines. This entails making sure that damage is reduced to component materials during important virus filtration, chromatography, or TFF processes.
Although peristaltic and lobe pumps have been most commonly used as pumping technologies for the above operations, it may be beneficial to consider using the quaternary diaphragm pump, as its function critically reduces the chances of pulsation or shear getting in the way of the reliability and efficacy of the end product.
References and Further Reading
- Video: “Quattroflow™: The New Standard in Biopharmaceutical Pump Excellence”
About Quattroflow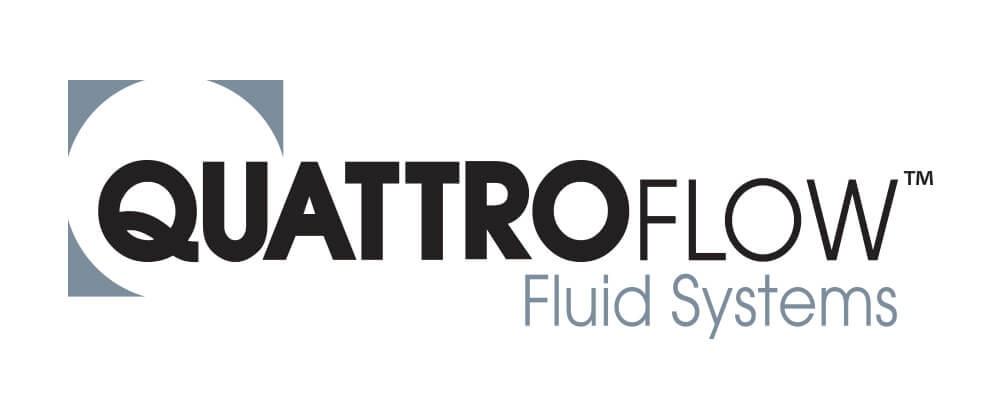
The Quattroflow story dates back to the 1990s. One of the founders was working in the filtration technology sector when he was in need of a pump to produce a protein solution. Together with the second company founder, an electric-specialist, they developed a diaphragm pump with four smooth-action pistons.
The start of the company was in the year 2000 using the location of the existing electrical installation company. At the beginning of 2004, they relocated to more comfortable premises.
In 2012 PSG, a business unit operating within the Fluid Solutions platform of Dover’s Engineered Systems a segment of Dover Corporation (NYSE: DOV) acquired Quattroflow. Quattroflow products are integrated into the German PSG operating company of Almatec, Duisburg.
Sponsored Content Policy: News-Medical.net publishes articles and related content that may be derived from sources where we have existing commercial relationships, provided such content adds value to the core editorial ethos of News-Medical.Net which is to educate and inform site visitors interested in medical research, science, medical devices, and treatments.