In the development and design of next-generation diagnostics and medical devices, photonics components have become key enablers. This trend has its roots in mature imaging technologies such as optical microscopy and endoscopy/colonoscopy, which has gained traction with the recent rise of molecular diagnostics and minimally invasive surgeries.
Now, through emerging applications such as laser ablation therapy, optogenetics, and optical coherence tomography (OCT), it is poised to accelerate.
In order to get a sense of the technology’s projected scale, note that during the current decade, the global market for photonics in life sciences and medical technology is projected to nearly double — growing from around $ 32 billion in 2011 to $ 56 billion in 2020 — according to market research.1
Yet, the more widespread utilization of photonics and optics technologies in medicine presents certain difficulties for medical device original equipment manufacturers (OEMs). The integration of these high-precision, complex components must be considered and carefully managed, from the earliest design phases through to production.
An ISO 13485 and 9001 certified supplier of electro-optical assemblies and optical components, Zygo Corporation, has been helping medical device OEMs integrate photonics capabilities successfully into their medical products for over 15 years.
Their extensive experience in optical design, assembly, and high-volume manufacturing enables them to provide precision optical components and systems on a build-to-print basis and also to shepherd them all the way through the development process, from concept to production.
Below, four of the most common mistakes medical device manufacturers make when attempting to incorporate optics and photonics into their designs, are discussed in detail.
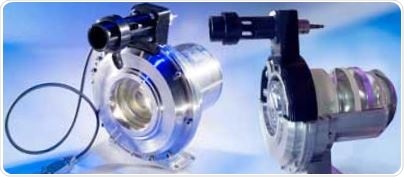
A custom built photonic medical device: An assembled laser surgery objective with a cutaway view of the lens stack. Image Credit: Zygo Corporation
Mistake #1: Incomplete tolerance analysis
Tolerance analysis and budgeting is the process of establishing the necessary design specifications for each component within the context of the whole system to ensure both the manufacturability and the best performance of the final product.
In a system that involves photonic components, from source to imaging, with all the spherical, flat, and aspherical precision optics in between, optical design tolerancing is absolutely vital.2
Mechanical and optical engineers must understand how tightly the size, tilt, thickness, surface figure, centering, and other parameters of the optics have to be controlled. Furthermore, it is just as important to analyze mechanical tolerances simultaneously, to avoid having one aspect of the design “hoard” the available tolerance budget at the expense of the other.
Unfortunately, a number of medical device OEMs carry out an incomplete tolerance analysis, failing to consider all of the aspects of their designs. Sometimes they do not have the engineering background to fully understand all of their optical requirements and performance drivers for their particular system needs.
Sometimes, from a biologics standpoint, they have an idea of what they are trying to achieve but they are not properly equipped to convert that concept into mechanical and optical requirements.
In cases where design work is outsourced, the contractor may understand the nominal system performance needs but may not be experienced in tolerancing a design for real-world assembly.
Incomplete tolerance analysis during design often results in problems regardless of the reason it occurs. Underspecifying optical tolerances can lead to performance shortfalls or problems during final assembly, either of which will need time-consuming and expensive design rework.
The cost and time ramifications are significantly amplified if the problem is not recognized until after clinical trials have begun, or worse yet, concluded, since every design alteration must be re-qualified by the Food and Drug Administration (FDA). Similarly, over-specifying optical tolerances can add unnecessary complexity, cost, and lead time to a project.
Medical device OEMs need to work with someone (internally or externally) who not only understands optical and mechanical systems design, but can also translate requirements into specifications that can be quantified, defined, and measured throughout the different stages of development in order to avoid situations such as these.
For instance, Zygo worked together with a medical device manufacturer on two beam expanders and an objective lens for use in an ophthalmic application. The company had engineers who understood optical system design very well, which made for a great working relationship.
They clearly understood and communicated the technical performance requirements but passed the entire optical design and tolerancing to Zygo, who ended up designing, verifying, and building the assemblies for them. The OEM was able to get its product to market very quickly as the product yield and performance had high success rates.
Mistake #2: Failing to fully inspect components
A lot of medical device OEMs think that if they review the datasheet for an off-the-shelf product (like optics or cameras) from a supplier, or submit a blueprint for a custom component to a machine shop, the parts they receive will match what is on the documentation precisely.
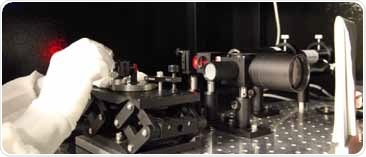
A measure of commitment and expertise: A custom-built interferometer may be what is needed to assure optical alignment of a lens assembly. Image Credit: Zygo Corporation
They trust suppliers to deliver components to spec, and so they neglect to carry out complete incoming quality control (IQC). During the inspection process, very subtle issues can be detected but the fundamental goal is to make sure that the components will work together properly in the final product.
It is crucial for medical OEMs to have the capability to make sure that what they are receiving is exactly what they asked for, particularly when the components have tight mechanical and optical tolerances.
Zygo has dealt with machine shops that do not possess the necessary equipment to establish if the finished opto-mechanical part matches the print. Even if a supplier does have the inspection capabilities required, it is incumbent upon OEMs to verify incoming part quality for themselves.
If they don’t, they run the risk that the parts won’t fit together in the product or achieve the alignment tolerances indicated by optical modeling. If a final system test was performed and it was discovered that the product was missing its performance targets, what was causing the problem would be a mystery.
So, the production line would need to be stopped, and root cause analysis be carried out, which can take a very long time. Next, once the faulty component was located, the entire lot may need to be scrapped and replaced, and the design reworked.
Such a situation was encountered by Zygo when assembling a device for analyzing proteins for a diagnostic OEM. One of the components of the opto-mechanical design (which was developed by another firm) was an off-the-shelf, high performance microscope objective lens.
Yet, the OEM did not create screening criteria for these objectives and did not inspect them upon receipt. Instead, they just expected that the parts would work.
Eventually, it was discovered that there was too much variability with these parts and Zygo had to create their own optical inspection requirement (pass/fail criteria) to establish which could be utilized in the system and which could not. The results: a lot of costly delays and wasted components.
Manufacturers must invest in specialized, expensive metrology equipment in order to inspect components fully, particularly optical components. A number of medical device manufacturers, including some of the largest OEMs, decide not to bring that kind of capability in house.
Instead, they work with a service provider that has the equipment needed to verify that the components they receive are what they expected. If parts fail inspection, they can be returned to the supplier long before they get to the production floor.
Mistake #3: Overlooking the impact of shipping
After going through the trouble of understanding the tolerance requirements and inspecting optical components carefully, it is important to consider the nature of the sensitive, precision-aligned product that is about to be shipped and how it should be packaged.
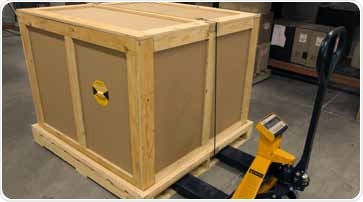
It worked when it left the factory. What then?. Image Credit: Zygo Corporation
When Zygo carries out an assembly of optics, the tolerance is at most about 10 microns of alignment precision, which is near the limit of human vision to see a detail, less than the width of a human hair. The optic is out of alignment and out of tolerance if it moves more than ten microns before it reaches its destination.
When handing their product over to the shipping company, that is the type of risk manufacturers take. OEMs should consider the level of packaging that is required as soon as the opto-mechanical tolerances are understood.
Once they know how much movement will be permitted in the alignment tolerance budget, OEMs can establish how to constrain the optics and what level of packaging is required. The precision of the packaging design should be consistent with the capabilities of the system to offset shock and vibration during shipping.
Misaligned optics and poor packaging design can cause severe consequences. Time could pass before the customer finds out that something is wrong with the product in the worst-case scenario, which for medical devices could lead to misdiagnosis, injury, or worse.
Some customers have extremely sophisticated internal test capabilities and can quickly establish whether or not the product conforms to their requirements. The product will be shipped back to the OEM to assess what went wrong and to either repair or replace it (and ship it all over again), if the product does not adhere to those standards.
Ensure that packaging design and analysis are part of the effort when working with a design or manufacturing house. For one medical customer, Zygo predesigned a shipping container for the optical assembly they were building for them and tested it with a dummy part.
That test showed that the G-forces associated with the typical shipping and delivery system would compromise the bonding of the optical components in the assembly. So, they reworked the packaging to account for that shipping stress, and every product shipped to that customer was in a specially designed shipping container. There have been no failures due to shipping to date.
Mistake #4: Supply chain management failure
Another area where manufacturers of photonic-enabled medical devices can go wrong is supplier selection. Many OEMs have procurement departments that handle supply chain management, but particularly when it comes to optical components, few of those groups have the engineering knowledge to vet a supplier properly.
They simply do not have the expertise on staff to understand what levels of precision a supplier can achieve. As a result of this, many OEMs end up presuming that because the supplier is an established optical fabrication house or machine shop, they can produce the quality of lens necessary for the OEM’s specific design.
What’s worse, manufacturers fall into the trap of basing supplier decisions solely on price. When it comes to choosing an optics supplier, the old adage, “you get what you pay for” certainly rings true.
The individuals that make purchasing decisions must have an understanding of the processes used to manufacture the types of optical components that their design needs. They must know what questions to ask and how to validate the response, for example by carrying out an on-site supplier audit.
Some questions to be considered are as follows:
- What type of equipment are they using?
- What can they measure?
- Does the project fall within their area of expertise?
- What are the supplier’s precision capabilities?
- What types of tolerances can they really hold?
- What technical resources do they have within their company?
- Do they have calibration certificates for those instruments?
Additionally, it is crucial to have dedicated resources that can receive (and inspect — see mistake #2 above) the finished components, and to be able to competently communicate with a supplier if problems should arise.
Even with the best suppliers it is inevitable that errors will happen, and the procurement team must have the resources available to quickly establish the root cause and work with the supplier to resolve the issue. On a related note, evaluating a supplier’s ability to handle not only the current level of demand, but also future volumes, is vital.
A small machine shop may be extremely diligent and precise when it comes to delivering a handful of prototype parts in a year, but can it maintain that level of service when clinical trials have finished and it is time to scale up to production volumes of hundreds or even thousands of parts per year?
At that point, changing suppliers can be a huge challenge for a medical device maker, which sometimes requires revalidation of the product. Zygo had an experience with a machine shop that was producing a high volume of components for one of their clients. After a while, they began to notice failures during their incoming quality check.
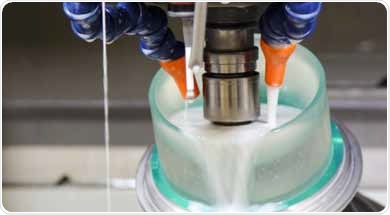
Sourcing parts externally involves surprisingly high levels of expertise in assessing vendors. This can be especially true in optics manufacturing. Image Credit: Zygo Corporation
Their supplier engineering was sent to the shop and it was found that the supplier was manufacturing lens housings (which required extremely high tolerances) in an environment which was not temperature controlled. This meant that the components only had a slim chance of being compliant and they ended up having to locate a new supplier.
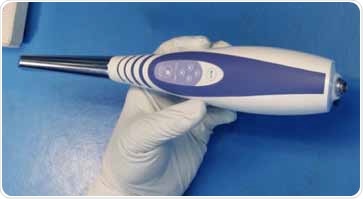
With a knowledgeable partner, optical subassemblies, or even final assemblies like this 3D dental imaging wand, including 20 optics and 3 imaging sensors in an autoclave compatible case, can be custom manufactured for you. Image Credit: Zygo Corporation
Conclusion
The path to market for photonics-enabled medical devices is extremely challenging. Prior to embarking on the development of a new design, OEMs must first make sure they have the right expertise to carry out a thorough tolerance analysis of the underlying optical components, fully inspect incoming parts, effectively manage their supply chain, and ship the finished product without misaligning the optics or otherwise degrading its performance.
For those who do not have the in-house resources, and would like to avoid these common pitfalls, the best option is to partner with an experienced firm who can help get new medical devices to the patients that require them as quickly and efficiently as possible.
References
- BMBF, SPECTARIS, VDMA, ZVEI (pub.), Photonics Industry Report 2013 (using a three-year average exchange rate of 1 euro to 1.32 U.S. dollars)
- John Filhaber, “How Wedge and Decenter Affect Aspheric Optics”, Photonics Spectra, October 1 2013, pp 44-47, Laurin Publishing.
Acknowledgments
Produced from materials originally authored by David Hill and Krista McEuen from Zygo Corporation.
About Zygo Corporation
ZYGO designs, manufactures, and distributes high-end optical systems and components for metrology and end-user applications. ZYGO's metrology systems are based on optical interferometry measuring
displacement, surface figure, and optical wavefront. Metrology and optical markets for end-user and OEM applications include semiconductor capital equipment, aerospace/defense, automotive, and research.
Now in its fourth decade, Zygo Corporation leverages its core competencies in metrology and optics to serve a worldwide customer base. Recognized as a valued partner by its customers for its innovation, technology, and responsiveness, the Company assists these customers in becoming leaders in their respective markets. Zygo Corporation's shares are listed on the NASDAQ market and traded under the symbol ZIGO. Headquartered in Middlefield, Connecticut, the Company employs approximately 525 people in offices throughout the world.
Sponsored Content Policy: News-Medical.net publishes articles and related content that may be derived from sources where we have existing commercial relationships, provided such content adds value to the core editorial ethos of News-Medical.Net which is to educate and inform site visitors interested in medical research, science, medical devices and treatments.