A heart monitor that registers every heartbeat of a patient, an invasive blood pressure monitor that takes critical vitals at regular intervals, a thermometer used to take a temperature during initial intake; while lifesaving in some cases, these devices are among the most widely used in almost all medical settings.
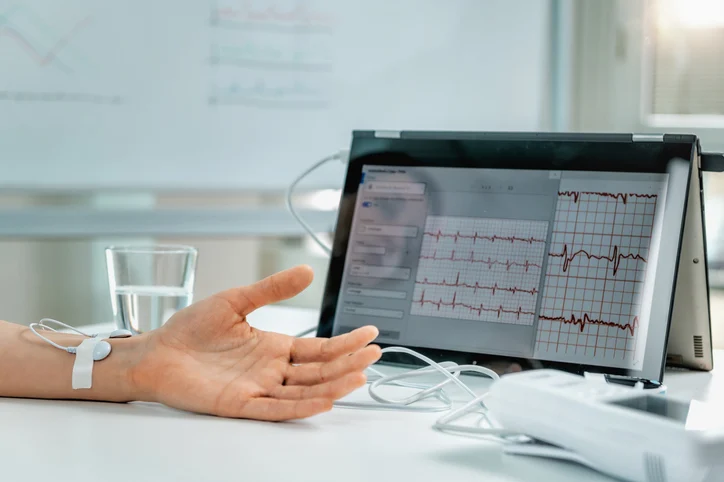
Image Credit: Amphenol Advanced Sensors
Like any piece of equipment utilized in patient care, there is no room for error in their measurements or performance.
Medical equipment has advanced significantly in recent years, with the devices currently used in all levels of patient care being more sophisticated than ever before.
Advances have also been made regarding treatment and its delivery, with remote patient care and wearable devices (once only considered possible in science fiction) now standard.
Custom-integrated medical sensor technology is the key to making the latest iteration of medical devices viable for patient care. When it comes to cost, the advanced sensors used in medical applications are not unlike those used elsewhere, such as in electric vehicles.
Like most cutting-edge technology, integrating customized sensors into a medical device requires investment, and premium technology comes at a premium price.
Still, for medical equipment manufacturers and those who buy them, sensor costs for their devices are a concern, so much so that it is among the first questions asked during an engagement.
Customized-integrated medical sensors as an investment
Before dissecting what drives the cost of custom medical device sensors, it is important to note that the price of every single product is relative to its value. Though customized sensor technology for medical devices may carry a bigger price tag, its value cannot be disputed.
A custom sensor means that the measurement technology is designed to work in sync with the user’s medical devices. There is little concern about if or when a retrofitted sensor will fail.
For manufacturers of medical devices, integrated healthcare sensors also provide an opportunity for innovation in their product line. Having an engineered solution that integrates custom sensors into an existing design allows the manufacturers to offer their products with new features and enhanced capabilities.
However, sensor technology for medical devices remains an investment. To that end, sensors are not a place to cut costs. The last thing any doctor – or patient receiving care – wants to discover is that the equipment used to take readings is outfitted with subpar sensor technology.
The integration of custom sensors into medical devices is an investment in:
- Accuracy – Medical devices must measure accurately. Custom sensors provide a higher level of precision to a device’s functionality as they are designed specifically for it, not retrofitted.
- Stability – A medical sensor must work reliably and consistently for the duration of its useful life. Custom-integrated medical sensors allow peace of mind as they will not lose pace while they are in service.
- Robustness – The effective application of sensors in healthcare means that they can survive in the environment they are within. This includes pressure, temperature, and vibration levels that can vary from benign to extreme. It also includes cleaning, as harsh solutions used for the sterilization of devices can lead to more damage than long-term use.
- Support – The best custom sensors are produced by experienced manufacturers with a proven track record. From design and engineering to customer support, top-tier custom sensor manufacturers deliver a higher level of service. In most cases, customers will develop a 1:1 relationship with their manufacturer that extends long past the initial purchase.
Factors driving the price of customized-integrated medical sensors
Like custom sensors employed in other applications, the costs of sensor technology in healthcare and OEM medical devices are driven by the following:
1. Design and engineering
Designing a patient monitoring sensor that is customized to function with a specific medical device is a task that demands a high level of expertise in the mechanics of the sensor and equipment, as well as in the application of these.
Everything, including the architecture, the materials, and the components of the sensor, must be considered. Engineering teams must also consider how their designs will interact with the hardware and software of a given medical device.
Since the sensor is not being purchased off the shelf, there is considerable time involved in working directly with the customer throughout the creation of their sensor.
The standard back-and-forth required to produce a customized sensor is no different from medical instrument design and development – it requires time and careful consideration.
The sensor development process is highly interactive, which enables a sensor manufacturer to work closely with the customer to understand their specific needs and produce a customized solution.
2. Components
One of the main contributors to the cost of a medical diagnostic sensor is the components utilized to build it.
In most cases, the parts employed have been carefully selected for their quality and performance capabilities. Although the cost of these components can vary substantially, it is important to remember what is being invested in – accuracy, stability, and robustness.
As the sensor is designed for a specific application, its components must be specially manufactured. This results in longer lead times that increase the overall production cost.
Some manufacturers can control this cost, namely those with in-house foundry services. Following the procurement of the raw materials, the manufacturers can build components in-house (from the sensor to the assembly), which removes the need to involve a third party.
Additionally, the complexity of the sensor design impacts component cost. The complexity of a medical sensor’s components depends on the type of sensor and its purpose.
For example, an electrocardiogram (ECG) sensor will have more complex components than a basic thermometer. Essentially, complex designs involve complex components, leading to higher costs.
3. Manufacturing
Unlike generic sensors, custom medical sensors need to be designed and assembled with maximum care and precision.
This includes everything from the creation of prototypes for testing to the production of the final product, and this must all meet the exacting healthcare standards. To meet these regulations, manufacturers need to use a variety of special processing methods, such as micro-machining and laser welding.
Medical sensors may also demand further treatments, such as plating or annealing, to enhance the durability and accuracy of the device. The whole manufacturing process is frequently subject to rigorous quality control tests to guarantee that all components comply with government-driven standards.
4. Testing
Like any piece of medical equipment, a device must first undergo extensive testing before being launched on the market and used in patient care.
Medical device testing is an extremely extensive process that is designed to ensure that devices used in patient care are safe, accurate, and reliable.
Testing of every aspect of the device is required, including the materials and components used and its performance under various simulated conditions.
Tests include electrical safety assessments such as the following:
- Ground continuity
- Insulation resistance
- Dielectric strength
- Environmental tests for factors such as temperature, vibration, and pressure
- Communication tests (to ensure the device can interface with other devices)
Testing is conducted in specialized labs where the conditions are precision controlled. Clinical trials may also be involved in the testing process in which a small group of patients uses a device to evaluate its performance in a real-world medical setting.
However, not all sensor manufacturers have the ability to complete testing in-house. Those that do not have to go elsewhere or put the onus on the user to find a solution.
5. Certifications
Device certifications come hand-in-hand with testing.
Perhaps more than any other device, those used in patient care are required to meet strict standards and regulations. Rightfully so – treating patients is the last place you want to introduce a faulty device. Certifications are the literal proof that a medical instrumentation system or device is up to standard.
Like most other devices, medical equipment is rarely produced without third-party components, even if it is a basic component like an LED screen. If just one component does not meet the standards, the entire device is deemed to be out of compliance.
The type of certifications required for a medical sensor will vary depending on where and how the sensor will be used. For example, although it is similar in many cases, the U.S. has different certifications than the European Union.
Getting the most for your money
Customized integrated medical sensors are costly, and it is worth asking an OEM sensor manufacturer about what comprises this cost. An experienced medical sensor manufacturer is an invaluable asset as they can help you get the most out of your investment.
Their expertise can help identify the right components for a sensor’s design and ensure that all relevant quality standards are met. They understand the importance of controlling costs while still providing a product that meets its intended purpose.
A reputable medical sensor manufacturer that is informed on the latest technologies, regulations, and certifications is invaluable and can ultimately streamline the entire sensor procurement and integration process.
A worthwhile investment
Lifesaving medical devices are invaluable, but cost is still a necessary consideration of medical devices and sensors.
Considering the design, engineering, components, manufacturing, testing, and certifications required, investing in a custom-integrated medical sensor is just that – an investment.
However, there is a guaranteed return from integrating custom sensors into a medical device, i.e., the ability of the equipment to perform exactly as it should and help healthcare professionals do their jobs effectively.
About Amphenol Advanced Sensors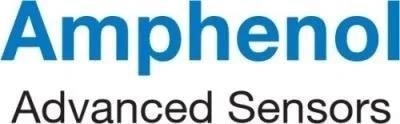
Amphenol Advanced Sensors, with its portfolio of industry-leading brands - Thermometrics, NovaSensor, Telaire, Protimeter and Kaye - is an innovator in advanced sensing technologies and innovative embedded measurement solutions customized for regulatory and applications, value by providing critical information for real-time decisions.
We offer domain expertise, rapid customization, world-class manufacturing capability and lasting customer relationships deliver the greatest value in cost of ownership to their customers.
Amphenol Advanced Sensors is a member of the USA-based Amphenol Corporation. With our own global presence we offer our customers exceptional technical support and service in the areas of development, production and distribution.
Sponsored Content Policy: News-Medical.net publishes articles and related content that may be derived from sources where we have existing commercial relationships, provided such content adds value to the core editorial ethos of News-Medical.Net which is to educate and inform site visitors interested in medical research, science, medical devices and treatments.