The pacemaker is a medical device that was initially introduced in 1958. At that time, the device used external components and was far from inconspicuous or convenient.
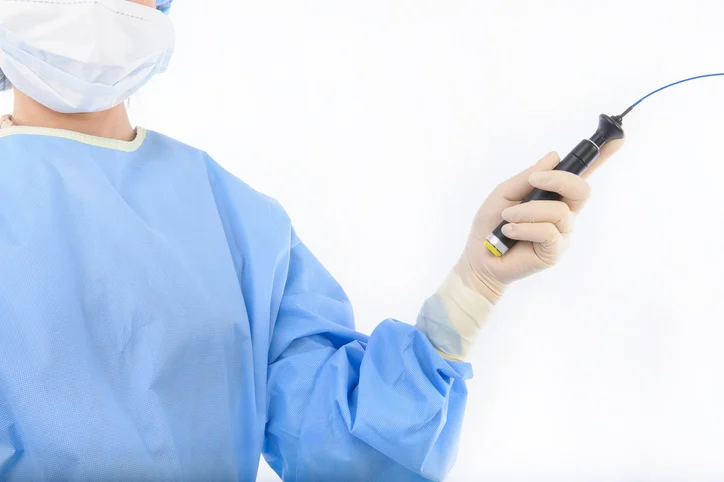
Image Credit: Amphenol Advanced Sensors
While it was still considered a lifesaving device, most components were located on the outside of the body. Patients who required a pacemaker had leads surgically implanted through their chest, which connected to a box approximately the size of a book. This box would then send small electrical jolts to the heart.
Within a few years, the pacemaker underwent a redesign, resulting in a much smaller and fully implantable device. Over the following decades, pacemakers continued to decrease in size, with the current version resembling a large pill and weighing less than a nickel.
The miniaturization of the pacemaker did not happen overnight, and this miniaturization is still an ongoing consideration in the design of medical equipment.
Reducing the size of medical devices is not merely a matter of making them smaller; it also necessitates the availability of advanced sensor technology to ensure accurate and effective functionality during the transition.
The manufacturing of these advanced sensors plays a crucial role in enabling the development of smaller medical devices.
For OEM medical device designers and manufacturers, custom miniature medical sensors are opening doors to improved device designs and upgraded functionality without compromise.
The how and where of custom miniature medical sensors
The aforementioned trends are particularly evident in the case of the pacemaker. When comparing the first fully implantable version of the pacemaker to the latest iteration, notable differences can be observed.
Apart from the reduction in size and weight, modern pacemakers are leadless and can be directly implanted into the heart. Although this transition took several decades, it exemplifies the continuous trend of size reduction in medical devices.
In addition to becoming smaller and more portable, medical devices are also benefiting from enhanced functionality. The pulse oximeter serves as a prime example of this trend. It is now small enough to fit on a patient's fingertip and combines the functionalities of measuring pulse rate and oxygen levels in one device.
The advancement of custom miniature sensor technology enables the intersection of smaller devices with uncompromised accuracy and functionality.
Custom miniature medical sensors find applications in various healthcare fields, ranging from temperature sensors to MEMS pressure sensors and other sensor types. These sensors are transforming numerous OEM medical equipment in terms of both size and function, including:
- Ablation catheters
- Cranial catheters
- Biopsy needles used in laser surgery
- IV fluid systems
- Ventilators
- In-home dialysis equipment
- CPAP O2 concentrators
As a result of these advancements, patients are getting the same quality of care in a much more convenient, less-disruptive manner. With customization options available for miniature sensors, they can be tailored to suit specific medical device applications.
Matching medical device size and function without compromise
In a perfect world, to miniaturize a medical device, all the design team would ideally need to do would be to design the device so that its components are smaller. However, this is far from the reality. This approach, although feasible, does not account for various factors that can affect the device's functionality and performance.
Shrinking the sensor technology for smaller devices also necessitates customization to ensure the effectiveness of the monitoring device. Therefore, working with an established OEM custom sensor manufacturer becomes crucial for developing smaller yet dependable medical devices.
A seasoned and knowledgeable custom sensor manufacturer understands all the design and performance challenges of creating miniature medical device sensors. A custom miniature medical sensor is not just made smaller; numerous significant considerations must be addressed in the process:
- Device size
- Intended lifespan
- Measurement area
- Environment
- Manufacturing
- Material selection
Device size
The smaller a medical device, the less available real estate there is for its components. In simplest terms, this can make for an extremely tight fit - sometimes to the micrometer.
Designing a custom sensor to suit these compact medical devices poses a significant challenge. It necessitates precise measurements and expertise in engineering. Engineers must consider various factors, such as the shape and material gauges, to ensure a perfect fit for the sensor within the given space.
Intended lifespan
Designing a sensor intended for non-disposable use, such as those found in pulse-ox meters, requires durability to withstand repeated usage. The engineered components must be robust enough to endure shocks or drops that may occur during regular operation.
Conversely, certain devices used in patient care, like invasive blood pressure sensors employed during surgery, are single-use and disposable.
For such devices, it is more logical to employ disposable medical sensors. While single-use sensors must meet performance standards for their specific applications, they do not necessitate the same considerations as those designed for long-term use.
Measurement area
In a way, the perception of sensor size affects the perceived magnitude of the monitored area, i.e., the smaller a sensor gets, the bigger the area it is monitoring seems. Think of it this way – as a child, getting to the top of a refrigerator seemed like climbing up Mt. Everest. As an adult, not so much.
As sensors shrink in size, the area they measure becomes more isolated. To ensure consistent and accurate results, the sensor must be adjusted accordingly to compensate for this discrepancy without compromising its performance. This adaptation allows the sensor to maintain robust functionality despite its reduced physical dimensions.
Environment
The design and manufacturing of a sensor heavily depend on the intended operating environment.
For example, wearable healthcare sensors that come into contact with bodily fluids, such as blood, require different construction methods compared to those that solely interact with the skin. Furthermore, sensors designed to be placed under the skin or within the body have additional criteria and design considerations.
In essence: the sensors used in medical devices must operate reliably in a wide range of temperatures, moisture levels, and other environmental factors that may directly impact performance.
Manufacturing
While numerous factors influence a medical device's sensor performance, accuracy takes precedence. Even a slight deviation from the nominal value raises concerns about the reliability of the measurements. The manufacturing process plays a crucial role in achieving accuracy.
The smaller the sensor gets, the more refined and precise its manufacturing needs to be. Miniaturization, in some respects, introduces a higher potential for manufacturing errors.
Consequently, while larger sensors and their assemblies may be suitable for manual assembly, smaller versions often require computer-driven automated manufacturing processes.
Material selection
There is no universal material used in every medical device. Instead, the choice of materials depends on the specific application and environmental requirements. Certain material combinations may be necessary to optimize the performance of the sensor.
For instance, in biomechanical sensors measuring strain or pressure, elastomers like silicone possess properties that facilitate accurate measurements. The selected material should also offer the appropriate compression and flexibility when applied to the device.
Customized medical sensors are able to effectively address these concerns. Additionally, careful consideration must be given to the materials used in medical sensor devices to avoid any potential leaching of toxins or substances into the body.
Custom miniature sensors: Big future for medical device
As medical devices continue to shrink in size, the significance of custom miniature medical sensors cannot be overlooked.
The ongoing trend of miniaturization is expected to persist, as it has in the past. The demand for precise measurements from compact yet dependable components has intensified, highlighting the growing significance of custom miniature sensors.
Thanks to advancements in sensor technology offered by reputable OEM sensor manufacturers, medical device manufacturers can now develop downsized products without compromising on accuracy or performance.
About Amphenol Advanced Sensors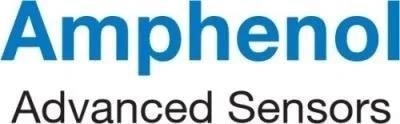
Amphenol Advanced Sensors, with its portfolio of industry-leading brands - Thermometrics, NovaSensor, Telaire, Protimeter and Kaye - is an innovator in advanced sensing technologies and innovative embedded measurement solutions customized for regulatory and applications, value by providing critical information for real-time decisions.
We offer domain expertise, rapid customization, world-class manufacturing capability and lasting customer relationships deliver the greatest value in cost of ownership to their customers.
Amphenol Advanced Sensors is a member of the USA-based Amphenol Corporation. With our own global presence we offer our customers exceptional technical support and service in the areas of development, production and distribution.
Sponsored Content Policy: News-Medical.net publishes articles and related content that may be derived from sources where we have existing commercial relationships, provided such content adds value to the core editorial ethos of News-Medical.Net which is to educate and inform site visitors interested in medical research, science, medical devices and treatments.