This article outlines guidelines for the testing of high pressure gases utilized in cleanrooms according to the cleanliness limits stated in the FDA cGMP guidelines, the ISO 14644-1 cleanroom classification standard, and the EU GMP Guidelines.
This article specifically relates to satisfying the air particle concentration limits of Class 100 (ISO 5) where product is exposed to the air environment.
Introduction
Guidelines for the testing of high pressure gases employed in cleanrooms according to the cleanliness limits derived from the ISO 14644-1 cleanroom classification standard, the FDA cGMP guidelines and the EU GMP Guidelines are supplied below.
Specifically, satisfying the air particle concentration limits of Class 100 (ISO 5) where product is exposed to the air environment. The biopharmaceutical industry routinely employs compressed gas in manufacturing operations.
Regulatory bodies like the FDA take interest in the quality of compressed gas coming into contact with pharmaceutical product, though no single best practice, standard, or guideline has been enforced specifically.
Manufacturers of biopharmaceuticals have used a number of methods for the routine monitoring of compressed gas, usually based upon a risk assessment with cleanliness limits derived from the ISO 14644-1 cleanroom classification standard.
cGMP FDA guidance to industry
In the FDA guidance, the scope of particle concentration limits is not just confined to the ambient air. Compressed gases like nitrogen, air, and carbon dioxide are routinely utilized in cleanrooms and are frequently used in overlaying or purging.
The FDA guidance states that these compressed gases should be of purity “equal to or better than that of the air in the environment into which the gas is introduced.” Section IV of the cGMP, Buildings and Facilities, addresses the requirement for appropriate air quality controls for aseptic processing areas of biopharmaceutical cleanrooms1.
These areas are defined as being vital, as particles are able to enter a product as an extraneous contaminant in addition to introducing a biological contamination risk by acting as a vehicle for microorganisms.
Table 1. Particle limits as defined in the FDA Guidance for Industry cGMP 2004. Source: Beckman Coulter Life Sciences
Clean area classification
(0.5 µm particles/ft3) |
ISO designationb |
0.5 particles/
m3 |
Microbiological active
air action
levelsc cfu/m3 |
Microbiological
settling plates
action levelsc,d
(diam. 90 mm; cfu/4 hours) |
100 |
5 |
3,520 |
1e |
1e |
1000 |
6 |
35,200 |
7 |
3 |
10,000 |
7 |
352,000 |
10 |
5 |
100,000 |
8 |
3,520,000 |
100 |
5 |
EU GMP Annex 1 is less specific than the FDA Guidance. Section 81 of the guide, which outlines the subject of materials needed to be passed into the clean area where aseptic work happens, indicates that non-combustible gases must be passed through micro-organism retentive filters2.
Section 60 states that gas filters (among other critical systems and components) should undergo planned maintenance and validation, and that their return to utilization should be approved.
The handling and filling of aseptically prepared products is addressed in section 33 of the EU GMP, and specifies that such activities should be carried out in a Grade A environment with a Grade B background.
Table 2. Particle limits as defined in EU Guidelines to Good Manufacturing Practice, Annex 1 2008. Source: Beckman Coulter Life Sciences
|
Maximum permitted number of particles per m3 equal to or greater than the tabulated size |
|
At rest |
|
In operation |
Grade |
0.5 µm |
5.0 µm |
0.5 µm |
5.0 µm |
A |
3 520 |
20 |
3 520 |
20 |
B |
3 520 |
29 |
3 52 000 |
2 900 |
C |
3 52 000 |
2 900 |
3 520 000 |
29 000 |
D |
3 520 000 |
29 000 |
Not defined |
Not defined |
The high pressure diffuser (HPD)
Usually, particle concentrations in compressed gases are quantified by utilizing conventional air particle counters which are routinely employed in cleanroom environmental monitoring schedules. Yet, direct connection of these instruments to high pressure gas lines is not usually possible.
A device known as a high pressure diffuser, or HPD, is necessary to decrease the pressure of the gas to be sampled to ambient so the gas can be sampled at the instrument’s standard flow rate while at the same time not introducing particulate contamination to the gas sample.
Together with the pressure reduction required, the HPD maintains isokinetic flow through to the device output to ensure that the size-distribution of any particles suspended in the gas is not skewed.
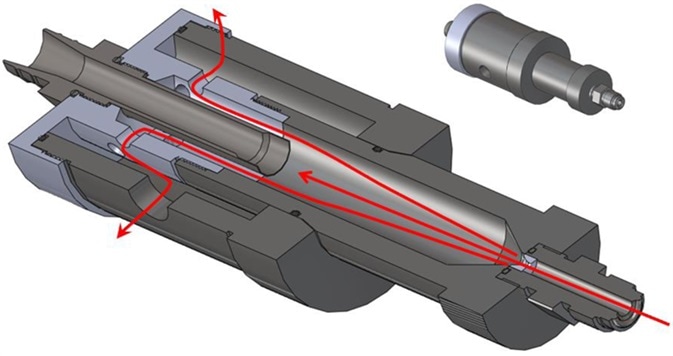
Figure 1. The MET ONE High Pressure Diffuser or HPD in cross section indicating the flow path to the Isokinetic sampling inlet and the exhaust. Image Credit: Beckman Coulter Life Sciences
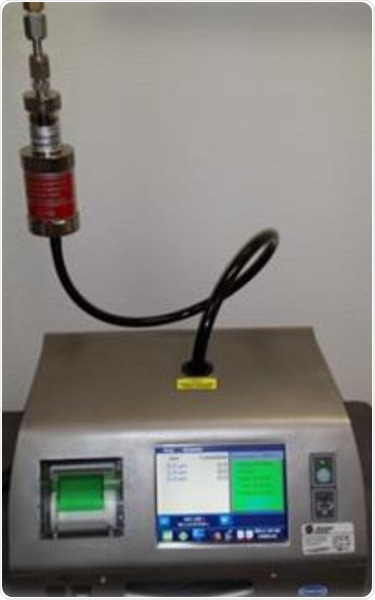
Figure 2. The MET ONE HPD connected to a MET ONE 3400 series counter and a gas line. Image Credit: Beckman Coulter Life Sciences
Methodology
The HPD is installed between the connection to the gas source and the inlet of the particle counter in order to sample high pressure gas lines. By diverting excess gas away from the sampling path, the presence of the HPD leads to a drop in line pressure, thus avoiding over pressurizing the particle counter’s sensor.
Excess gas is diverted via a port in the HPD chamber either away to a different location via tubing or directly into the environment. It is crucial that the HPD is supplied with gas within the specified operating range.
Running the HPD at a pressure that is too high will lead to an inaccurate particle count whereas operating under the lower limit will lead to air being drawn back through the exhaust port and contaminating the gas sample.
The necessity to adjust the particle counter’s sample flow control system to compensate for the density of the selected gas is a second requisite for compressed gas particle counting applications.
For accurate volumetric sampling to be attained in accordance with ISO 14644 and to comply with the ISO 21501-4 calibration standard for air particle counters, sampling at the true mass flow rate is necessary. The MET ONE 3400 series makes this necessary adjustment extremely simple and intuitive for the operator.
MET ONE Model 3400 series gas selection option
In this model, gas monitoring is made simple via the gas option, together with the appropriate High Pressure Diffuser (HPD). The user simply chooses the gas required from a pull-down list on the 3400 interface.
With the appropriate gas to be sampled chosen, the pump control system is adjusted automatically to make sure that a 1 CFM flow rate is maintained for the chosen gas.
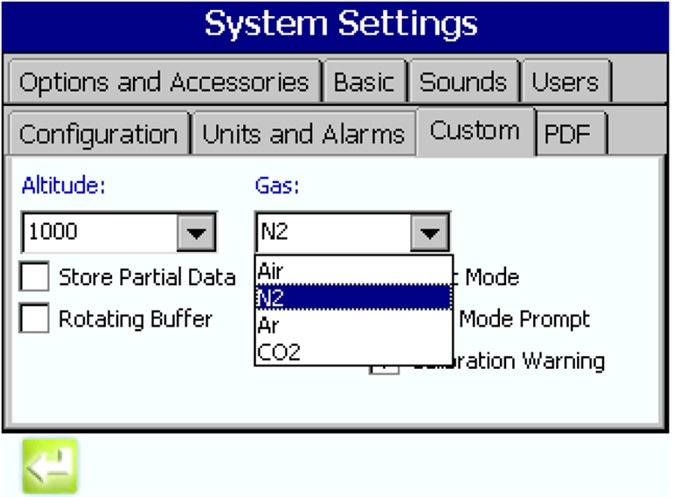
Figure 3. Selecting the gas to be monitored via a sample drop-down on the MET ONE 3400 user interface. Image Credit: Beckman Coulter Life Sciences
Gas sampling procedure
- Turn the Met ONE 3400 particle counter on.
- Program the number and size of samples required.
- Set the Count Mode to Counts per Cubic meter.
- Program the concentration alarm limits per either Grade A or ISO 5 (note that the per cubic meter limits for 0.5 um are the same for both, but that Grade A also specifies limits at 5.0 µm
- Attach the tubing to the exhaust port of the HPD to minimize contamination to the surrounding environment.
- Verify that gas pressure at the sample point is within the HPD manufacturer’s specification (outlined in the user manual) by utilizing a calibrated pressure sensor.
- Open the sample point fully and purge the HPD for around 30 seconds.
- Connect the HPD to the MET ONE 3400 sample inlet nozzle with the tubing supplied.
- Permit gas to flow through the HPD and into the MET ONE 3400 Particle counter.
- Let the system run for a minute as a purge of the complete assembly.
- Begin sampling by pressing the run button on the MET ONE 3400.
- Close the valve on the compressed gas source when the sampling recipe has finished.
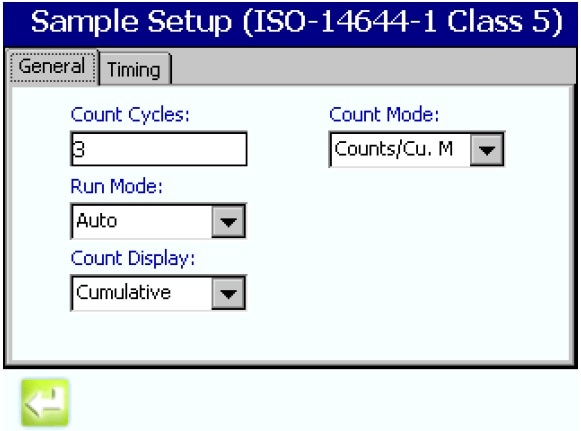
Figure 4. Setting the sampling parameters. Image Credit: Beckman Coulter Life Sciences
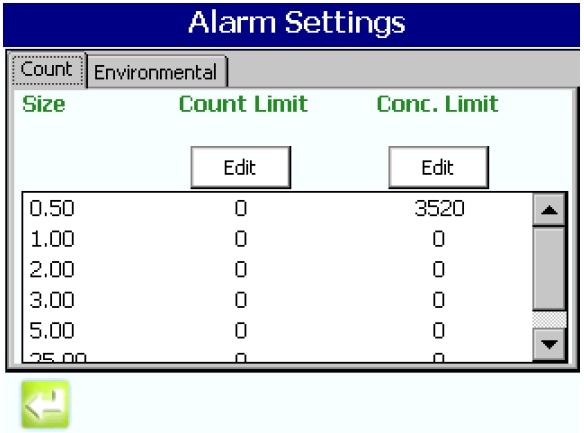
Figure 5. Setting the alarm limits per ISO 14644. Image Credit: Beckman Coulter Life Sciences
Reporting the results
Usually, particle results are reported as an average of a number of sample runs. The below example of a particle measurement on a compressed Nitrogen line shows the MET ONE 3400 series support for traditional paper printout, Excel and PDF compatible files.
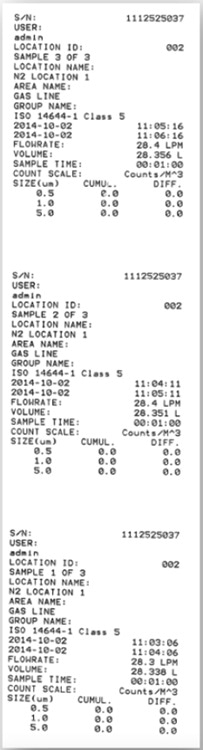
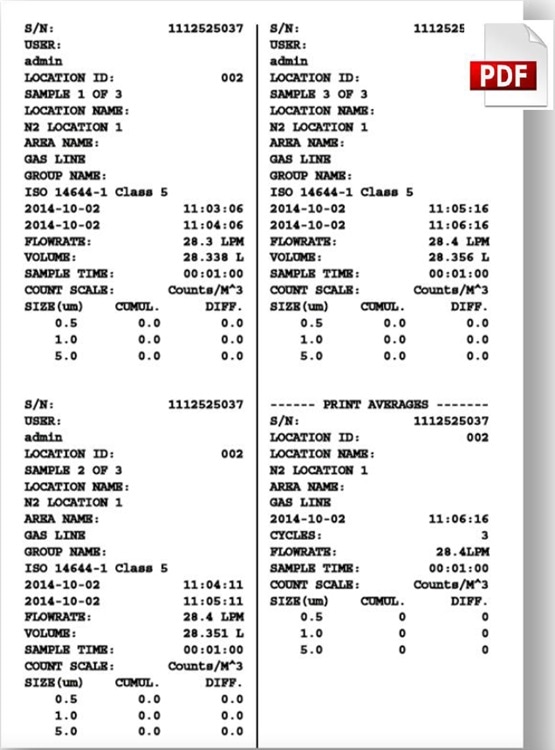

Figure 6,7,8. Instrument printout of a compressed Nitrogen test based upon 3 samples and an average. PDF and Excel outputs are also available on the MET ONE 3400 series portable particle counters. Image Credit: Beckman Coulter Life Sciences
Choosing a particle counter for gas sampling
To perform particle testing of compressed gas lines using the MET ONE 3400 series is simple. Ordering a new 3400 with gas calibration can be achieved with a single part number. Six versions in the series are available which include gas calibrations for air, Carbon Dioxide (CO2), Nitrogen (N2), and Argon (Ar).
Table 3. Source: Beckman Coulter Life Sciences
MET ONE 3400 portable
w/gas calibrations PN |
Description |
2088900-06 |
MET ONE 3413 0.3 micron, 1 CFM |
2088900-07 |
MET ONE 3413 0.3 micron, 1 CFM with WIFI |
2088900-08 |
MET ONE 3415 0.5 micron, 1 CFM |
2088900-09 |
MET ONE 3415 0.5 micron, 1 CFM with WIFI |
Table 4. Source: Beckman Coulter Life Sciences
High pressure diffuser |
Description |
2080732-13 |
1 CFM HPD 3/8" Barb |
A high pressure diffuser is needed in addition to the MET ONE 3400 particle counter. Users who already possess existing MET ONE 3400 series particle counters that would like to add gas calibration to their instruments can order this as a factory service choice.
Table 5. Source: Beckman Coulter Life Sciences
Calibration |
Description |
CAL_GAS_3400 |
Gas calibrations for 3400 series particle counters |
Conclusion
Used together with the MET ONE 3400 High Pressure Diffuser, the MET ONE 3400 series with gas calibration option make testing of high purity compressed gas to ISO 14644-1 easy, eliminating the potential for sampling errors associated with flow rate, and ensuring compliance to the ISO 21501-1 calibration standard.
References
- Guidance for Industry. Sterile Drug Products Produced by Aseptic Processing — Current Good Manufacturing Practice. Food and Drug Administration, 2004.
- EU Good Manufacturing Practice, Annex 1: Manufacture of Sterile Medicinal Products
About Beckman Coulter Life Sciences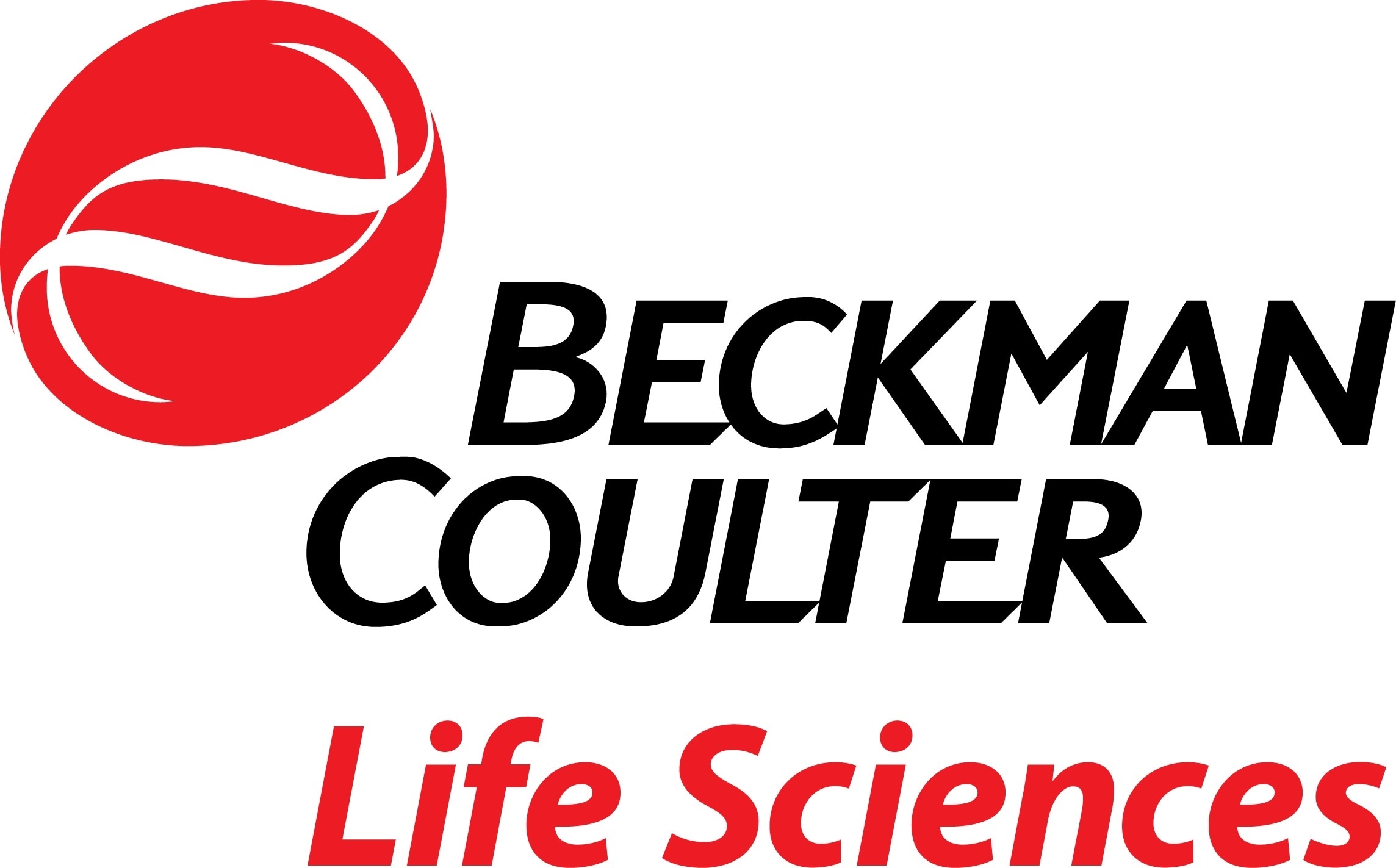
Beckman Coulter Life Sciences is dedicated to empowering discovery and scientific breakthroughs. The company’s global leadership and world-class service and support delivers sophisticated instrument systems, reagents and services to life science researchers in academic and commercial laboratories, enabling new discoveries in biology-based research and development.
A leader in centrifugation and flow cytometry, Beckman Coulter has long been an innovator in particle characterization and laboratory automation, and its products are used at the forefront of important areas of investigation, including genomics and proteomics.
Primary activity / Product lines
- Flow Cytometry
- Centrifugation
- Particle Counting and Characterization
- Liquid Handling and Robotics
- Nucleic Acid Sample Preparation
Sponsored Content Policy: News-Medical.net publishes articles and related content that may be derived from sources where we have existing commercial relationships, provided such content adds value to the core editorial ethos of News-Medical.Net which is to educate and inform site visitors interested in medical research, science, medical devices and treatments.