The wide-ranging scope and the sheer number of regulatory requirements faced by producers of medical devices and pharmaceuticals have placed a significant strain on an organization’s internal resources due to the commissioning of new systems and keeping these in compliance.
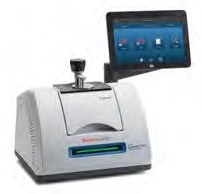
Thermo Scientific™ Nicolet™ Summit FTIR spectrometer. Image Credit: Thermo Fisher Scientific – Materials & Structural Analysis
These industries are not the only ones impacted, however. Consumer products, food and beverage and manufacturing industries must all ensure robust quality and safety across their whole range of processes.
Quality standards or regulations must be adhered to, but there is also a noteworthy cost of poor quality in terms of rejected lots, loss of purchasing contracts or even legal action in the worst-case scenario.
Organizations must employ a secure system comprised of a comprehensive toolset of FDA-compliant 21 CFR Part 111 tools, qualification packages, audit trails, certification services and operator training around the regulatory environment.
Organizations must also ensure they are making measurements in line with relevant regulations, ensuring that verification of system performance is performed as a seamless part of the process.
Despite this number of requirements, using the right system can ensure that data is safe and secure.
The Thermo Scientific™ Nicolet™ Summit FTIR spectrometer is one such fully secure system. It is comprised of three robust software applications: Security Administration, Audit Manager and Thermo Scientific™ OMNIC™ Paradigm Software (Figure 1).
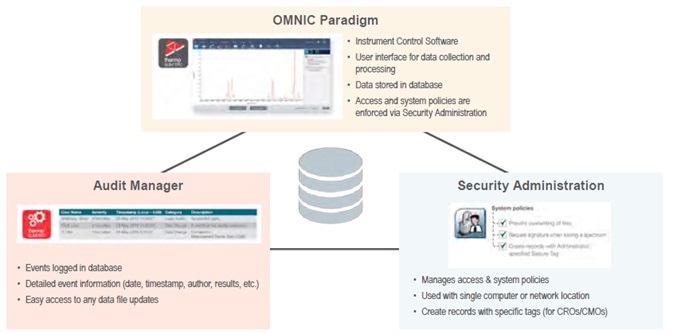
Figure 1. Security suite and instrument control. Image Credit: Thermo Fisher Scientific – Materials & Structural Analysis
The Audit Manager and Security Administration applications are also referred to as the Thermo Scientific Security Suite. The Audit Manager’s role is to log events and store this information in an SQL or user-specific database, allowing users to access detailed event information and tracking on demand.
The Audit Manager software captures system event information, for example, when a user logged in, when a spectrum was collected or when data was saved. Once this data is stored, the software provides an array of easy filtering tools to allow users to quickly find events by date, computer ID, username and more.
Audit Manager also provides details on additional events, including specific spectral processing information, providing a single location for an auditor to review.
Security Administration is responsible for controlling access and system policies for each individual user. A new secure tagging feature enables CROs and CMOs to provide data access to users based on a secure tag which can be different for each individual piece of data.
The Security Administration software affords lab managers the ability to control which user has access to what data, allowing them to enable or disable specific commands and features within the instrument software.
It can also prompt and require technicians or scientists to digitally sign their data to ensure this complies with 21 CFR Part 11 regulations.
The software can manage multiple instruments from a single installation, for example, a distributed configuration – making it ideal for use in larger labs.
The instrument control software (OMNIC Paradigm) is responsible for managing data collection, sample analysis and workflow creation, storing the full range of spectral data in a secure relational database.
The Thermo Scientific OMNIC Paradigm instrument control software can be employed in data collection: acquiring a range of spectral data, metadata about the author (including processing history, tags, and results) and comprehensive audit trail information. It can also be used to analyze samples and create workflows.
Like the Audit Manager software, the OMNIC Paradigm Software stores all spectral data in a database, ensuring robust security and data storage flexibility. Users can assign tags to specific measurements, making querying data straightforward and accessible.
The OMNIC Paradigm Software utilizes the MariaDB® relational database by default, but users can select the database of choice from a supported list (Table 1).
Table 1. Relational databases compatible with OMNIC Software. Source: Thermo Fisher Scientific – Materials & Structural Analysis
Database |
Supported Versions |
Aurora DB |
MySQL 5.6
MySQL 5.7 |
MariaDB* |
10.0
10.1
10.2
10.3 |
Oracle |
11g Release 2
12c Release 1
12c Release 2 18c |
SQL Server |
2012
2014
2016
2017 |
*The Maria DB is the default database.
Discussion
Benefits of a database
There are numerous benefits to storing data in a database – in terms of both daily use and auditing purposes. Databases are specifically designed to organize and retrieve large data sets, allowing these to be filtered by author, time and instrument name.
Databases enable metadata to be automatically linked to related spectral data, significantly improving and strengthening the audit trail. The audit trail will alert users to a spectrum changing in the software provided while also highlighting what changes were made to the spectrum.
The use of databases will also ensure that files are always in sync – there is no risk of duplicates or orphans.
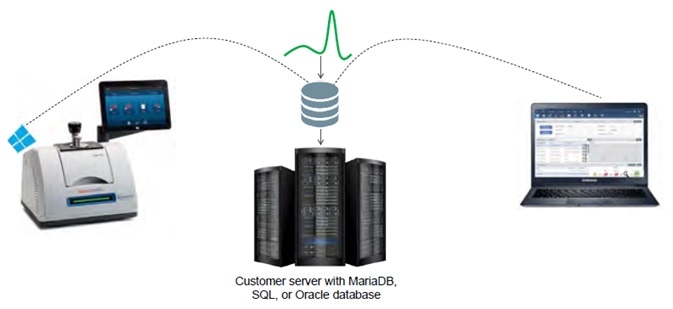
Figure 2. The Remote Database option. Image Credit: Thermo Fisher Scientific – Materials & Structural Analysis
The OMNIC Paradigm software’s Remote Database option allows users to configure the database to reside in another location rather than on the instrument itself. Storing the database on a company server already equipped with appropriate security measures can improve security and better control data integrity (Figure 2).
Only a user with appropriate administrator-provided permissions can access that remote data. Connecting multiple instruments to a single remote database allows users to review data from several systems via remote access.
Taking advantage of compliance services
It is imperative that documented evidence is available to verify the correct installation and function of intended hardware and software.
Another key element of this process involves access to trained service engineers that are able to offer Installation Qualification/Operational Qualification (IQ/OQ) services as part of an instrument’s installation, after moving to another location or any time that it is required.
Thermo Fisher Scientific’s instrument validation and qualification services are offered via Unity Lab Services.
Compliance documentation
IQ documents provide confirmation that a system has arrived and is installed and connected correctly. These documents verify that all parts have been included, that the instrument arrived undamaged and that the installation environment is appropriate for the instrument.
OQ documents confirm that the system operates according to its design and specifications, verifying that the hardware and software work effectively together and that spectral data collection is accurate.
This process also involves ensuring that the Security Suite software is installed correctly, that appropriate event logging is performed and that security policies are verified.
Performing system qualification checks
Working in a regulated environment necessitates regular checks to confirm that an instrument is performing as anticipated – usually undertaken daily.
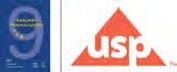
Image Credit: Thermo Fisher Scientific – Materials & Structural Analysis
This performance check is typically referred to as ‘System Qualification’ and should be undertaken using methods outlined in the US, Japanese, Chinese and European Pharmacopeias.
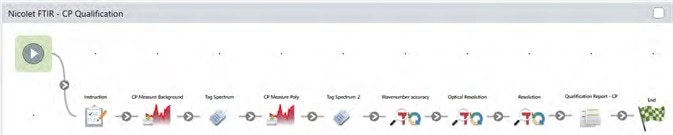
Figure 3. Example qualification workflow on the Nicolet FTIR. Image Credit: Thermo Fisher Scientific – Materials & Structural Analysis
The OMNIC Paradigm Software features a range of automated analysis procedures to ensure a spectrometer is compliant with all performance requirements specified in Pharmacopeia documents (Figure 3).
Each instrument should include its own traceable internal polystyrene standard, meaning that instrument performance can be checked with a single button press.
Conclusions
Ensuring regulatory compliance places an additional burden on internal resources, regardless of an organization’s products or processes. Integrating a database with advanced instrument control and audit management capabilities shifts the most laborious compliance tasks to a more automated, computer-based system.
Opting to use a fully secured system, such as the Nicolet Summit FTIR spectrometer, Thermo Scientific Security Suite and OMNIC™ Paradigm Software, eases the burden of regulatory compliance by automatically capturing the data required to guarantee complete compliance.
Acknowledgments
Produced from materials originally authored by Matthew Gundlach and Katherine Paulsen from Thermo Fisher Scientific.
About Thermo Fisher Scientific – Materials & Structural Analysis
Thermo Fisher Materials and Structural Analysis products give you outstanding capabilities in materials science research and development. Driving innovation and productivity, their portfolio of scientific instruments enable the design, characterization and lab-to-production scale of materials used throughout industry.
Sponsored Content Policy: News-Medical.net publishes articles and related content that may be derived from sources where we have existing commercial relationships, provided such content adds value to the core editorial ethos of News-Medical.Net which is to educate and inform site visitors interested in medical research, science, medical devices and treatments.